How technology can improve safety in lifting operations
30 September 2024
At the recent Tower Cranes North America conference Casey Savlov, executive vice president at Vita Industrial, explained how technology can be used to improve safety in lifting operations. Niamh Marriott reports.
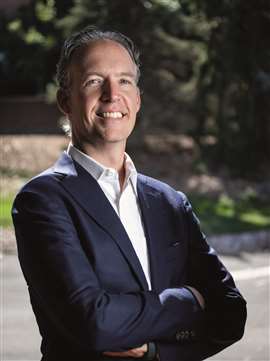
Vita Industrial started out as an aerospace company for the US military.
“There’s an issue when you rescue people with evacuation helicopters, you lower a litter basket and those baskets swing, right? Our founder, [Caleb Carr] was doing a mission off a mountain medical evacuation with his mentor, who had heart problems. They called a helicopter to evacuate him but could not do it fast enough because the baskets were spinning so much. Unfortunately, the mentor went into cardiac arrest and died.”
After this, Carr began work on systems for the US military at university, developing technology to stabilise baskets under helicopters and he decided to try and develop the same thing for loads on construction cranes.
Leveraging technology
For the construction industry, the use of cranes and heavy lifting equipment is both essential and fraught with risk.
Traditional methods of controlling a load, which often involve workers managing taglines and operating close to heavy loads, have historically presented significant safety challenges. Recent advances in technology, however, are changing how these operations are conducted, dramatically improving both safety and productivity, Savlov claims.
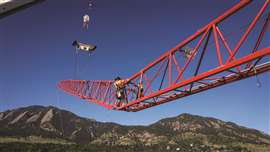
“Managing loads is not easy, it’s very costly, it’s very risky. We have a standard of using taglines to manage these loads. And let me be very clear, I am not, nor is our company, suggesting that you don’t use taglines. We just believe with the advancement in technology there could be safer, faster, smarter ways than just only having a tagline.
Evolution of operations
Savlov provides an overview of how Vita’s technology is reshaping crane operations.
Showing a slide of a tower crane disassembly he says, “This is how you dismantle a tower crane. Now what you’ll notice there’s this little device at the top... you’ll notice there are no 400- or 500-foot taglines. There’s nobody running around this congested site risking a slip, trip or fall.”
The technology in question is a unit suspended from the crane that eliminates the need for traditional taglines (ropes used to stabilise loads). By removing these, the risks of slips, trips and falls – common hazards on congested construction sites – are significantly reduced.
One example Savlov discusses involves the dismantling of a tower crane at a congested site in California, USA. Here, a single operator using a remote control was able to manoeuvre the load with precision, bringing it down between two buildings without the need for multiple workers handling taglines.
Savlov notes, “There’s one guy... using a remote control, which will automatically rotate this load between those two buildings and bring that down in less than nine minutes.” This not only enhanced safety but also reduced the time needed for the operation.
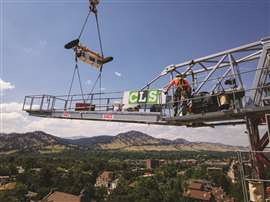
Stability in motion
The ability to keep loads stable during lifts is another significant safety improvement offered by modern crane technology. Savlov describes a project in Minneapolis, USA, where the technology kept a crane’s load “completely stable,” allowing the crane operator to move faster and more efficiently.
“The load’s completely stable, it’s not going to rotate,” he says. This stability is crucial, especially in environments where precision is essential, such as when placing large forms in narrow spaces.
At this site workers previously spent 18 to 21 minutes completing tasks that now take just 4 to 6 minutes thanks to the technology. “They now drop those forms in minutes,” Savlov says. This not only accelerates project timelines but also minimises the time workers spend near potentially dangerous loads, thereby reducing the likelihood of accidents.
When the wind blows
Wind is a notorious challenge in crane operations, often forcing work to halt due to safety concerns. New technologies like Vita’s, however, are helping to mitigate these issues. Savlov recounts a project on San Francisco, USA’s Treasure Island, where high winds regularly posed a significant challenge.
Despite being rated for winds up to 35 miles per hour (57 km/h), the crane operator would typically stop work at around 16 or 17 mph (26 to 28 km/h) due to safety concerns. After implementing the new load control technology, however, the operator found that he could continue working even in higher winds, thanks to the load’s increased stability.
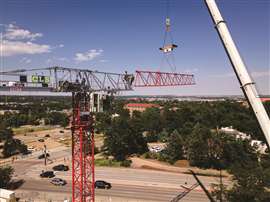
As Savlov describes, “As those winds are howling, that load is completely locked into position as he is rotating it to where he needs to go.” This technological advance not only reduces downtime but also prevents accidents that could occur if taglines were used in high wind conditions. The result is a safer, more efficient operation that keeps projects on schedule even in challenging weather.
Economic impact
While safety is the primary benefit, the economic advantages of using this technology are also significant. Savlov shares a story about a construction site in London, where two identical cranes were operating under different conditions. One crane, equipped with the technology, could continue working despite adverse weather, while the other had to be shut down for safety.
“The safety team said you cannot use that second crane. It’s too dangerous today with the weather, but that crane that has the technology you can use all day long,” Savlov explains.
This difference in operational capability not only improves safety but also increases productivity, as work can continue uninterrupted. For contractors, this means more efficient use of equipment and labour, leading to cost savings and potentially higher profit margins.
Reducing damage
Another important aspect of Vita’s crane technology is its ability to reduce property damage. Traditional lifting methods often result in loads swinging or rotating uncontrollably, which can lead to costly damage.
“A lot of their panels get damaged from the tagline smacking them in some of the conditions,” Savlov notes. By stabilising the load and controlling its movement with precision, the technology minimises these risks, leading to fewer claims and lower insurance costs.
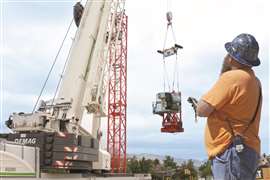
Potential
The technology Savlov discusses is not limited to any specific type of crane or lifting operation. It can be adapted to a wide range of equipment, from tower cranes to mobile cranes, and used in various construction scenarios.
As the construction industry continues to embrace these innovations, Savlov says the potential for even greater safety improvement is enormous. He concludes with a forward-looking statement, “This is just the beginning of what we’re doing. In another month or so, we’ll have some more exciting announcements of what we’re going to bring to the market.”
Integrating advanced technology in crane operations is a game-changer for the construction industry. By enhancing stability, reducing the need for taglines, and allowing for safe operation in challenging conditions, these innovations are significantly improving safety on construction sites.
As Savlov puts it, the ultimate goal is to ensure workers go home safely to their families every day. With these technological advancements, that goal is increasingly within reach.