How technology and onsite equipment is reducing construction’s carbon footprint
08 November 2021
Leila Steed looks at how technology is transforming onsite construction equipment and helping contractors reduce their carbon footprint
The cost of running a construction site has always been a concern. Historically, that cost has mainly been defined in terms of money.
Now, however, as the whole of Europe bands together to achieve its net-zero-carbon goal, the word ‘cost’ is increasingly being used to refer to the toll construction activities take on our environment.
While much of the focus on sustainability and low carbon technology is being placed on equipment such as excavators and wheeled loaders, it is in the onsite equipment sector where it has been most successfully incorporated.
Often among the easiest and cheapest ways for construction firms to lower their carbon footprint, the latest onsite equipment on the market also represents one of the most practical ways of reducing carbon emissions.
Generators
Take generators, for example. New innovations from manufacturers have led to the release of a range of low-emission products that can help reduce both the environmental and financial cost of construction operations.
Most recently, Caterpillar launched the 200kVA Cat XQP200 mobile generator set – the company’s first Stage V compliant mobile power solution for engines used in non-road mobile machinery.
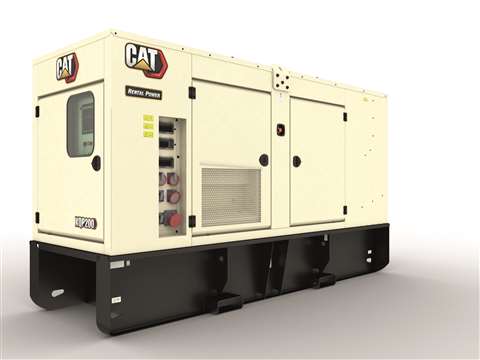
Designed with a dual-wall, open-top fuel tank that contains spills, the Cat XQP200 generator allows users to switch between 50 and 60Hz and across a range of voltages, and can handle the varying loads required by construction, mining and oil and gas applications.
“The Cat XQP200 mobile generator set leverages numerous technological advances from Caterpillar’s equipment portfolio to deliver the consistent performance, reliability and fuel efficiency that improve the competitiveness and productivity of mobile equipment users,” says Tom Caldwell, global general manager for electric power rental solutions at Caterpillar.
“At the same time, it helps our customers meet their sustainability goals while addressing current regulatory standards, which is especially timely as growing numbers of European municipalities institute low emission zones.”
Indeed, the increasing concerns around carbon emissions has led some companies to move to newer power sources.
Construction equipment provider Loxam recently signed a deal with French specialist Energy Observer Developments (EODev) to introduce a hydrogen powered generator into the European market.
The 80kW GEH2, which uses a Toyota fuel cell and a lithium-ion phosphate battery and produces no pollution, CO2 emissions or particulate matter.
The unit, which has a footprint of less than 4m2, includes a “peak shaving” mode that enables it to connect to the power grid and a 4G connection. This allows the unit’s location, usage data and hydrogen reserve status to be continuously monitored online.
According to Loxam, the addition of the GEH2 is part of its ongoing efforts to move away from diesel and petrol powertrain products.
Battery powered storage units
Himoinsa’s new EHR Battery Power unit can be used with standard diesel or gas-powered generators, as well as being linked to mains power grids and solar panels.
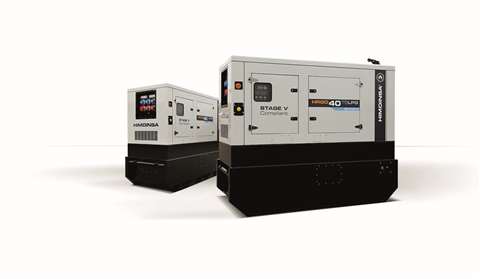
Launched just this month, the new battery-powered genset is available in single phase 10kVA and three phase variations with 15, 30 and 45kVA nominal power.
Offering zero emissions and zero noise, the EHR stores and distributes energy from standard generator units using lithium ferro phosphate batteries. This enables users to reduce the amount of time a standard generator is run for, thereby lowering fuel usage and operating costs.
According to Himoinsa, the EHR includes its HICORE System, which ensures energy is used efficiently.
“This smartgrid controller selects the most favourable energy source for each charging condition, achieving the greenest and efficient energy solution”, says the manufacturer.
Alongside the batteries, which can be fully charged in less than 1.5 hours, the unit comprises an inverter, control unit, power connections and solar MC4 connectors.
The unit provides users with a choice of Plug & Play, Low load, Load sharing, Peak saving and UPS modes for different applications.
With Europe’s drive towards net zero now unstoppable, this level of flexibility has become increasingly important in other types of onsite equipment as well.
Construction site lighting towers
A case in point is Lind’s new All-In-One Beacon LED Tower. It is described as a single lighting asset that replaces the need for three separate lighting units.
This means it can function as an all-in-one generator powered light tower, a diffused light tower and an electric tower.
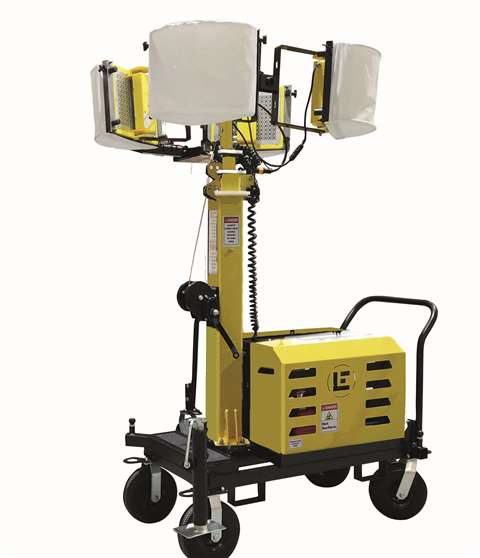
Sean Vandoorselaer, CEO of American manufacturer Lind Equipment , says, “It’s first and foremost a durable and tough remote generator light tower that replaces the bulky, traditional 4x1000W metal halide towers.
“Secondly, it can work as a no-glare diffuser light tower for nighttime road work or events that require diffused lighting. All that’s needed for this mode is to simply clip on the diffuser frames to each light head to create no-glare diffused light.
“Thirdly, it can work as an electric powered light tower off an external power source for indoor and outdoor applications.”
Because the Beacon LED Tower does not require a generator, Lind says it halves the cost of a traditional generator powered light tower.
Currently available in the UK, France, Spain and Norway, Vandoorselaer says the model means contractors will no longer need different products for each of these applications.
---
Similarly, lighting tower manufacturer Generac Mobile has also introduced an all-in-one model. However, unlike Lind’s Beacon LED Tower, Generac’s lighting tower represents an “all-round change” that is said to provide a “solution for any kind of need”.
The company’s new CUBE PRO model incorporates a “whole new technology” that allows contractors to choose from diesel, battery, hybrid or plug-in power modes at the flip of a switch.
The lighting tower model features an integrated diesel generator and a rechargeable battery pack.
While the diesel generator and battery pack can each provide 100% of the power supply, the CUBE PRO also includes Generac’s Hybrid System, which enables it to alternate battery working cycles with diesel recharging cycles.
“Some customers will ask for a full-battery model because they need total silence and zero carbon emission; some others will need the power of a generator-driven model,” says Generac.
Additionally, the unit can also be plugged into an external power source to give contractors even greater flexibility when it comes to power options.
With ability to be flexible of key importance on construction sites, recent improvements to air compressors are now providing contractors with more options, while helping to reduce emissions on site while.
Air compressors
For example, Atlas Copco has recently updated its 8 Series range of portable air compressors with new technology and new engines, to meet Europe’s Stage V emissions regulations.
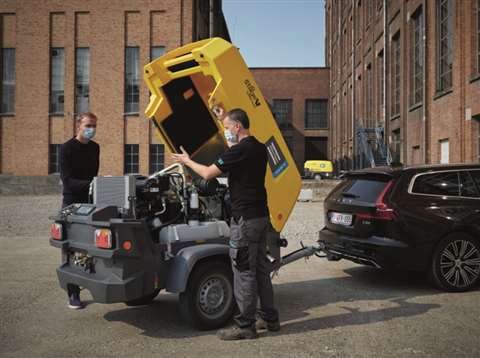
The 8 Series range consists of 11 machines that are now fitted with the latest Stage V compliant engines from Kubota. The smaller diesel engines in the range, which include the D902 and D1105 power units, offer reduced CO2 and NOx emissions and a 25% increase in fuel efficiency.
Rodolfo Reimberg, vice president marketing portable compressors and tools at Atlas Copco, says, “The updated range allows construction managers to comply with Stage V regulations while keeping the known benefits of our 8 Series such as lightweight, integrated generators, and HardHat PE hood.”
“Additionally, this range gives users better control over their energy consumption, helping them achieve a more cost-efficient, sustainable, and productive way of working.”
Many of the 8 Series models also include a new Xc2003 controller, which features the manufacturer’s PACE (Pressure Adjusted Through Cognitive Electronics) and ECO-mode apps.
ECO-mode allows operators to further lower fuel consumption by up to 50% when in idling mode during downtime.
According to Atlas Copco, the air compressors also incorporate its Air Element design. This means that most of the 8 Series machines weigh under 750kg and can be towed behind a car without needing a special driving licence.
Meanwhile, the new Mobilair M255 portable compressor from German manufacturer Kaeser offers a maximum available flow rate of 25.5 m³/min and delivers pressures between 6 and 14 bar.
Described as “ideal for drilling, quarrying or blasting work”, the model features a Cummins 210kW engine with a diesel particulate filter and an SCR system.
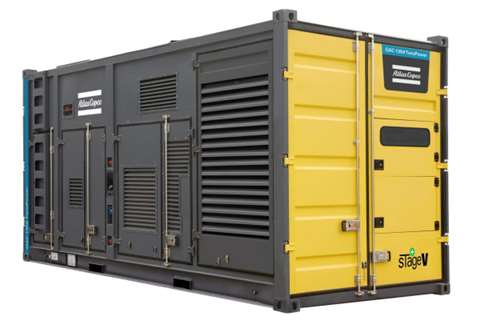
The M255 also incorporates an energy-saving fan and air filter with safety elements, as well as a new oil separation system that uses easily replaceable cartridges for reduced maintenance times.
Kaeser’s largest oil-injected portable compressor, it includes a rotary switch and a touch display, which operators can use even when wearing gloves. It also includes the company’s new Sigma Control Mobil 2 (SCM 2) compressor controller for use with multiple stationary systems in a compressor station.