Aquajet hydrodemolition robot completes ‘challenging’ cement plant project
14 April 2023
A cement plant in La Robla, Spain needed to repair a 100-metre-tall, 16-metre-diametre concrete silo during an annual maintenance shutdown. The walls of the silo were held together with rebar on the outer and inner layers of its concrete, but nothing connected the two, causing the concrete to deteriorate and fall.
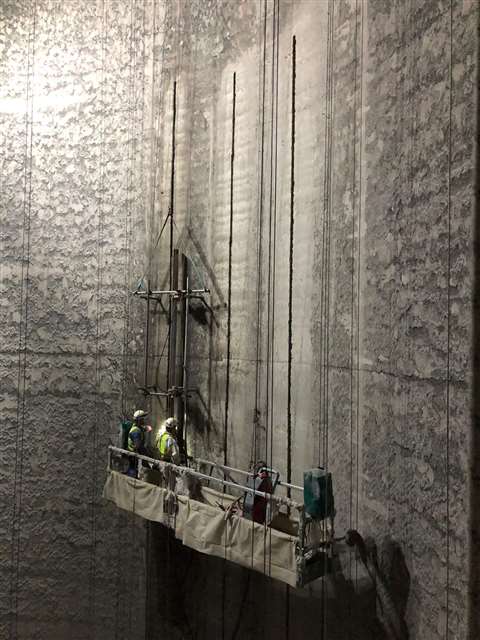
A company specializing in concrete and structure repair was hired to fix the silo in 2019, but only the lower portion of the silo was repaired due to limited time. Two years later, Jose Rodriguez and his new company, Fixen Structural Services, won the contract to complete the repair using Aquajet’s Ergo Hydrodemolition robot.
The Ergo is a compact Hydrodemolition robot, with a climber that attaches to any standard scaffolding pipes and robotically moves along it, providing four times the power of a hand lance. Exerting 1,000 newtons of reaction force, the Ergo removes concrete or other material to a consistent preset depth.
The cement plant’s maintenance shutdown had a four-week deadline, and Fixen proposed that a robotic Hydrodemolition method along with the use of hanging platforms would complete the work by the deadline.
But with any job, there are challenges. With the silo’s height of 100 metres, rather than using a traditional scaffolding system, the Fixen team decided to opt for a much safer motorized hanging platform to comfortably stand on and bring additional equipment up with them as they worked on the structure.
Additionally, the Fixen crew needed approximately 100 metres of constant water pressure to ensure a successful Hydrodemolition repair. To achieve this, Fixen used a 2,500 bar Hammelman pump with a flow rate of 24 litres per minute. The pump, situated on the ground for the duration of the project, incorporated a 120 metre long, 3,000 bar pressure, hose extending up the structure to the Ergo. The Ergo controller was placed on a hanging platform, following the Ergo climber on each 4 metre vertical section. The cement plant provided the water and discarded the blast water into a cistern on-site.
The final step of the repair was to fill the open spaces with fluid mortar to complete the section. The team achieved a production rate of one metre per minute, removing two 45-metre vertical sections of concrete each day.
Fixen says that the use of technology such as the Ergo Hydrodemolition robot allowed them to complete challenging repairs quickly, safely, and effectively.