Benninghoven creates wood dust burner to make ‘green asphalt’
19 July 2024
Germany’s ‘first’ nearly carbon-free asphalt mixing plant started production in Bavaria following a collaboration between Benninghoven and road construction company Altomünster.
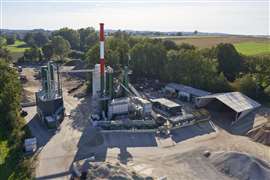
The Wirtgen Group brand said the new facility – located in Aichach, Bavaria, Germany – is a next step in creating net-zero “green asphalt”.
Paving the way for a more sustainable product is the use of wood dust instead of oil as an energy source. Previously, the plant used about 600,000 litres of heating oil to produce an annual output of 60,000 litres of asphalt, which resulted in emissions of 1,800 tonnes of CO2.
Contractor and operator of a mixing plant in Aichach, Germany, Christian Schweiger approached Benninghoven more than four years ago to collaborate on a plan to use renewables as a power source.
Benninghoven installed a power limiter that helps reduce burner performance to 12 MW/h. If the plant expands, the burner is designed with enough reserve capacity to scale performance to match – an aspect that Schweiger signalled to Benninghoven as being vital to the project.
Retrofitting Benninghoven’s EVO JET burner
The company’s EVO JET multi-fuel burner was modified to accept wood dust as an energy source. Wood pellets, chippings and wood dust can be used as starting raw material, which must be ground to a predefined particle size to ensure efficient heating in the burner, said Wirtgen Group. A supply fan and dosing unit were also added for high-precision feeding the wood dust into the burner.
“In September 2023, the first virtually carbon-free asphalt mixing plant is now in operation, fired by wood dust instead of heating oil,” said Wirtgen Group.
A specialist company was brought in to supply the preprocessing system needed to produce wood dust of a requisite quality.
For Altomünster, the new investment is already paying for itself, said Wirtgen Group.
“At the start of the project, we assumed that sustainability will be an important topic for the future, but the fact that switching to wood dust has already cut our costs by around 20% was definitely a pleasant surprise,” added Schweiger.
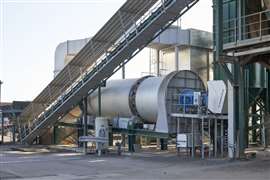
Looking ahead, Schweiger said he’s curious what is next in terms of sustainable asphalt production solutions.
“Using wood as a fuel is obviously only an interim solution,” he said. “I do get the impression that, here in Germany, we tend to approach technical issues as perfectionists rather than just taking the better option, though it might not be perfect.”
Germany’s ‘first’ green asphalt plant spent years in regulatory purgatory
Despite the goal of the collaboration rooted in reducing CO2 emissions – therefore reducing public harm – Wirtgen Group noted the timeline from idea to production required years of regulatory approval.
“The undertaking was designed as a research and development project from the outset,” said Wirtgen Group. “As a first step, Schweiger set to work on obtaining the government grants, fire safety appraisals, and noise/emissions reports – a time-consuming approvals process.”
Wirtgen Group said the “lack of experience” on the part of regulators caused the lengthy wait.
“Legislation from local government included a number of requirements, such as ensuring continuous emissions measurement and restrictions on burner capacity,” explained Wirtgen Group.
Regarding compliance, the group said the most important standard to meet was TA-Luft, which became law in Germany in 2021.
TA-Luft is the German Technical Instruction on Air Quality Control, which dictates various requirements for companies in regulating air pollution and emissions.
“Four weeks after burner installation, the design engineering team from Benninghoven got emissions figures to a level 50% below the TA-Luft requirements, with continuous measurement,” stated Wirtgen Group. “Follow-up checks from a TÜV appraiser team [inspectors] confirmed these values in full, making Benninghoven the only manufacturer capable of achieving – and guaranteeing – compliance with limit values for a wood dust burner plant.”
For more information on Benninghoven’s eco-asphalt plants, watch the video below.