Bosch Rexroth VP offers insights into eLion portfolio at Bauma 2022
15 November 2022
At this year’s Bauma trade fair, Bosch Rexroth took the opportunity to introduce its new eLion component and service portfolio. In a nutshell, the eLion series is an end-to-end range of high-voltage hardware solutions intended to both reduce fossil fuel usage and improve operational efficiencies. The components are suitable for use in virtually any off-highway vehicle.
“We already have internal combustion engines covered, be it gas, hydrogen or diesel,” explained Dr Alexander Flaig, senior vice president, Mobile Hydraulics, in an interview with DPI on the Bosch Rexroth stand. “Using our factory automation hardware as a starting point, it has taken about four years to bring together this new product portfolio for the mobile business. We think that’s quite a good turnaround, in an industry which can be slow moving in terms of technology adoption.”
Within that portfolio there is a broad selection of new introductions, ranging from electric motors and inverters, through to tailored gearboxes, hydraulics and related software.
“Everything included in the eLion portfolio has been developed from the ground up,” said Flaig. “Taking products out of different business sectors doesn’t really work in this area. It would have been pure luck if anything from another division was a perfect fit, so we decided that developing unique, specific products for the portfolio was the right way to go.”
Continuing, Flaig noted that such technology transfer could really only happen if the original product platform had been designed for off-highway applications, due to the demands of the machines and the operating environment. He said that as Bosch Rexroth is familiar with the machine types and the applications in which they are used, it helped with taking the electrified systems from concept through to production. It also helps to ensure that the new technology will be a good fit for OEM machine manufacturers.
“In the early days, customers would simply remove a diesel engine and replace that with an electric motor. We’re moving away from that now, with specific motors and peripherals designed for particular machines.”
According to Flaig, Bosch Rexroth now offers four different electric motor ranges, with motor speed being the defining feature. From those four units, he said that there are about 80 power delivery solutions which can be assembled from the related ‘kits’ of matching components.
“That is complemented with a choice of three inverter sizes, which serves as basically the electronic control of the system,” he added. “The portfolio covers everything from 20 to 200 kW, peak of 400 kW. We think that these will be suitable for about 90% of the applications machine makers are addressing.”
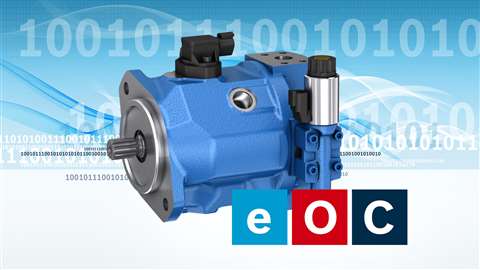
In addition to the electrification portfolio, another new introduction was the eOC (Electronic Open Circuit) hydraulic architecture, a hydraulics and related software package supporting dynamic control of work processes. A series of other companies have launched similar products to the eOC hydraulic component series, but Flaig noted a key differentiator in the systems produced by Bosch Rexroth.
“Control wise, getting an open circuit system to be stable in operation is not that easy. I’ve seen it in academia, called secondary control, which is mostly used in fluid power. I think the way control theory is applied in this open circuit is unique to us. Using real-time assessment of the dynamics, we have developed a system which can prevent any related oscillation. That’s the challenge, ramping up the power without any oscillation in a matter of milliseconds, but we have managed to do that.”
The November/December issue of Diesel Progress International will feature more interviews from Bauma 2022.