What are the latest innovations in the attachments market?
01 August 2024
Excavator attachments – the dangers, the cost savings and the latest products on the market.
Earlier this year, the United Kingdom’s safety regulator, the Health & Safety Executive (HSE), filed charges against yet another construction contractor for health and safety breaches, which in this case, led to the death of an employee.
A lengthy investigation found that the company in question – a specialist in the demolition sector, had failed to ensure a safe working method for its team when moving equipment.
While loading an excavator fitted with a grab onto a low-loader trailer for transport, the team failed to fully engage the quick hitch connection between the excavator and the attachment.
The grab subsequently disconnected from the machine during the loading process, and crushed a 24-year-old site worker.
Following the company’s crown court appearance and the issuing of a €208,000 fine, HSE inspector Joanne Williams said: “This tragic death serves as an important reminder that workers need to be trained and that there is always the potential for an attachment to fall during the operation of excavators.
“Employers need to ensure that work practices are maintained to keep workers away from the danger areas during lifting activities.”
Keeping workers safe
While some may think that this type of incident is rare, the unintentional dropping of an attachment due to it not being properly connected the carrier, is not so rare – and as this case illustrates, can have devastating consequences.
When it comes to safety, all attachments manufacturers have their own systems for ensuring a solid connection between the coupler and the work tool, but a new technology from Steelwrist may be a gamechanger.
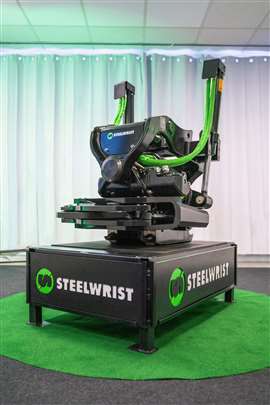
The Swedish company recently released its third-generation XTR20 tiltrotator, which comes as standard with the OEM’s latest break-through product; the LockSense system.
Described as “a new leap” in safety technology, LockSense is a sensor-based front pin hook system.
The system comprises locking wedges that slide into place around the attachment’s connection point, and then twist into a locked position.
Inside the wedges, wireless sensors detect when the locked position is fully achieved.
The technology then sends a radio signal to the machine’s onboard computer system, which provides the machine operator with both visual and auditory confirmations that the work tool connection is complete, secure and reliable.
While the creation of such safety technology will no doubt make the worksite safer, other recent equipment developments will also have a big impact.
Electric attachments for electric carriers
A new product that hit the construction tools sector just weeks ago could mean significant changes for attachment users and buyers.
The LEKA Toras 35 electric hammer from Finland-based company Lekatech, recently made its commercial market debut. It was among the standout products presented by OEMs at this year’s Hillhead exhibition in the United Kingdom.
Believed to be the first electric powered hydraulic hammer in the world, its development represents what could be the start of another monumental shift in the construction equipment industry.
The LEKA Toras 35 electric hammer is built on the company’s patented linear electric motor technology and is the result of many years of dedicated research and development.
It is designed for use with electric powered carrier machines and, according to Lekatech, can deliver “huge benefits on urban construction projects and in quarry or mine environments, above or below ground”.
Standout performance features of the Toras 35 include a 70% reduction in energy use when factoring in the overall energy consumption of the equipment, and double the blow impact energy of hydraulic hammers of the same size.
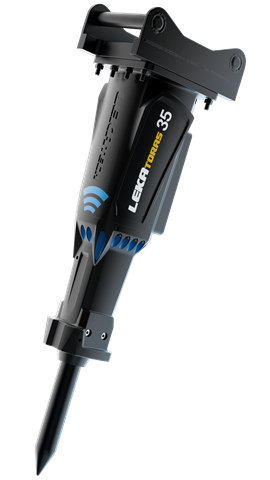
It also offers a 98% reduction in oil consumption compared to hydraulic hammers.
Changing legislation
While the commercialisation of such a unit heralds the start of more electric attachment releases, these are thought to be some time away, despite European governments continuing to push forward Net Zero targets. Why is this?
Put simply, although European governments are implementing policies to curb global warming, distinct and detailed legislation has so far been primarily focused on constructors and building methodologies, not on the equipment needed to help meet sustainability targets.
In an interview with our sister publication, Demolition & Recycling International, Lekatech’s CEO Antti Antilla, spoke candidly about the situation: “The legislation is not up to date when it comes to the electric transition.
“For example, the CE marking for our product – and obviously we are under the machine directive, but when it comes to individual requirements, it’s not clear how to show and prove that.
Antti explains: “In our case, we’ve really had to dig down to a wider scope to form our own understanding of the machine directive, so that we can answer key questions about the directive.
“Such as; what does it require from us? And which different standards do we need to pull together and fulfil, in order to be in-line with the machine directive?
“That’s the kind of work we’ve had to do, and there’s still different situations depending on how connected the equipment is.
“And when it comes to the safety of machines, that’s one area of legislation that is not yet clear.
Antti adds: “There is another aspect too, which is to do with the interaction between the carrier machine and our machine: How should we regulate that?
“We have had discussions with OEMs to find out how they see the directive and the standard that is in place, so that we can determine the meaning of this together.”
Despite being left somewhat in the dark when it comes to equipment legislation for equipment not powered by standard combustion and hydraulic technolgies, OEMs are continuing to produce machines that contribute to construction becoming more sustainable.
Task specific attachments
Producers of hydraulic work tools are creating attachments that are becoming ever more task-specific, so they can carry out tasks as efficiently as possible.
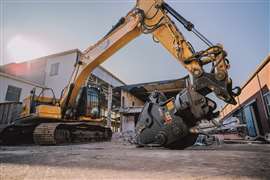
Take Genesis, for example. It has now introduced the GRP 480 hydraulic mobile shear, which is designed exclusively for processing rebar.
Developed in response to customer requests, the GRP 480 Rebar Processor attachment has an extra-large pivot group designed to provide the durability needed to handle daily rebar processing.
It features a 24-inch jaw opening with a 26-inch jaw depth and fits up to 21-tonne carriers.
Similarly, for mini excavators, Genesis has released the M7 Concrete Cracker attachment for concrete processing.
Fitting up to 11-tonne carriers, the M7 weighs just over half a tonne and offers a 27-inch jaw opening with a 19-inch jaw depth.
Genesis says, “The M7 efficiently processes concrete with a hydraulic booster that increases power and speed and a fully guarded cylinder rod that’s protected from debris.”
Quick couplers
Whatever their function, the key to all attachments – as we learned at the beginning of this article – is the connection to the excavator.
And this year, industry giant Caterpillar was among those to contribute something to this product type.
In May, the company introduced three Cat Hydraulic Connecting CW (HCCW) coupler models, which allow operators to quickly switch between hydraulic attachments from the cab.
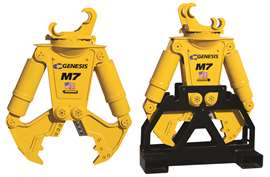
And of course, the standout feature of the HCCW20, HCCW30 and HCCW40 models is the Locking Control system.
The system comprises sensor technology that measures the locking wedge position and indicates the coupling status to the operator.
Caterpillar says, “multiple electronic and mechanical measures help to secure the attachment, even in the event of pressure loss.”
It adds that “visual and audible confirmations inside the cab inform the operator of successful attachment connection,” to help safeguard construction operatives on the jobsite.