Building efficiency: The cloud-based technologies boosting construction productivity

Partner Content produced by KHL Content Studio
27 February 2025
As one of the major drivers of economic growth in North America, there is a clear need for the construction industry to improve its levels of productivity levels.
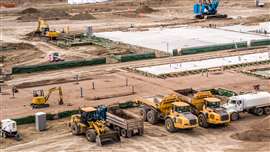
Where manufacturing has benefited from average growth of around 1.7% a year since the 1990s, productivity levels in construction have barely picked up at all.
This is perhaps an unfair comparison, when one considers the structured nature of manufacturing, with materials proceeding in an orderly fashion down production lines, and undergoing the same processes time and again.
By contrast, construction sites are never the same twice. Not only does the location change, but the on-site teams, the machines, the materials and the applications tend to be unique to each project.
Adopting the right technology
One of the biggest boosts to manufacturing in recent years has been the exponential increase in the adoption of digital technology solutions.
While digital technology is also prevalent on construction sites, it’s fair to say that its full potential is yet to be realized. As an example, while Building Information Modeling is being widely adopted, many construction professionals would admit they are only scratching the surface with this complex system.
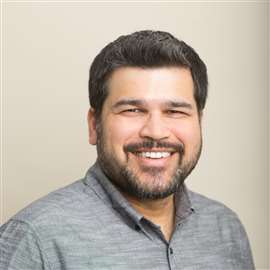
It’s clear that things need to change in construction and the rapid development of cloud-based technology has resulted in some easy-to-implement and easy-to-use solutions to many of construction’s age-old challenges.
Dhanush Balachandran, founder and CEO of Sortly, an inventory management software company that services a number of industries, including construction, believes technology – especially cloud-based solutions – offers powerful tools to manage the variables that have held back productivity for so long.
“By ensuring a single source of truth and eliminating version control issues,” he says, “these platforms provide all stakeholders – whether on-site, in a warehouse, or in the office – with access to the same, real-time information. This approach benefits not only inventory management but also other critical construction tools, such as BIM software and project management platforms.”
Marshaling assets
According to Balachandran, many construction businesses – even large, reputable companies – continue to rely on manual processes, using simple spreadsheets and even pen and paper to keep track of progress and inventory. He insists that “today’s construction professionals must be as adept at leveraging smart technology as they are with traditional tools.”
Given the industry’s propensity to stick with age-old methodologies, it’s easy to see why a major challenge that construction has been facing for a number of years is the retention of project data.
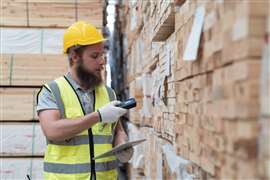
In fact, recent studies have shown that up to 95% of this data is unnecessarily lost when the construction phase of a project comes to an end.
However, Sortly’s director of product marketing, Vicky Venegas, believes this is set to change.
“We are seeing a shift towards project data being maintained more consistently,” she says. “The adoption of digital tools like project and inventory management tech not only provides visibility, but also the structure for teams to build habits around organization that weren’t as feasible before.
“Now, any administrator can jump in and see which steps have not been taken, what data or information is still missing, and can quickly follow up with teams when projects are over, to make sure that all of the information is added before closing.”
Balachandran adds, “Technology solutions enable a level of data capture and analysis that’s simply unattainable with manual processes. This digital record helps construction owners to identify trends and patterns over time, ultimately leading to more informed and strategic decision-making.”
Tools for the job
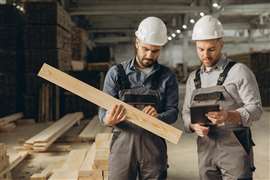
That decision-making for a busy project manager includes ensuring the right equipment is available on site at the right time. Maximizing machine uptime is a constant challenge for industry professionals who absolutely recognize the difference optimal equipment usage can make to the bottom line.
Balachandran describes this as “a perfect example of how tech can optimize inventory. Many construction businesses are using our software to do more than just track inventory; it helps them actually use what they have.
“Say a crew needs a specific tool; instead of buying a new one, the software can show them they already have it in storage – they just didn’t know it. Inventory solutions can also help optimize pick list processes to make sure the right materials and tools are packed up and ready to go for each day’s work, so nothing gets lost or left behind.”
In general, the loss of some tools and materials has been seen as ‘par for the course’ on a construction project – a dent in the profit margin that simply has to be accepted.
However, Venegas believes those days should be behind us. She says, “Where I see digital tools helping control some of the variables is through location tracking. Instead of having your crew roaming around searching for the right equipment, tools, or materials, they can look at their phone and know exactly where to find what they need.”
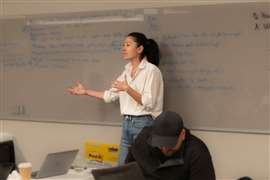
Venegas says this level of detail can help save tens of thousands of dollars a year, simply by reducing the number of times work is paused to search for inventory.
Balachandran agrees, saying loss prevention has become a priority for the industry, and keeping a digital record of who’s using what and when is a huge step towards making everyone more accountable.
“As well as owners having a clear picture of what’s happening across the crew,” he says, “It also helps clear up situations where something that appears to have been stolen, may have just been misplaced.
“Plus, it makes receiving deliveries much smoother, so owners know exactly what materials they have and what they’re worth, across all their job sites.”
Location, location, location
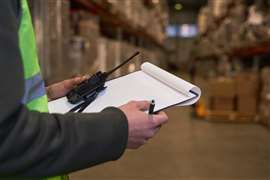
In some cases, project managers are overseeing multiple sites at the same time, which can exponentially increase the logistical headache.
The latest cloud-based inventory software solutions, however, promise to make equipment tracking as straightforward with 20 active job sites as it is with one.
The benefits of this scalability will not be lost on rental companies, with valuable assets potentially operating on construction sites far and wide, nor on those managing inventory in warehouses and storage facilities.
Balachandran says many of Sortly’s customers rely on its mobile barcode scanning feature to check equipment in and out, so it’s never lost or misplaced. “There’s a digital record of who used it and when,” he says, “which is particularly important for extremely high-value machinery and equipment.”
Set for change
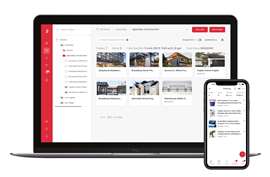
Construction has been labeled a conservative industry, resistant to change. The truth is more complex; construction businesses are looking for straightforward technology that can be quickly implemented and make an immediate difference to the bottom line.
On this point, Venegas says, “Where I see technology helping improve overall efficiency is in helping construction projects stick to the budget and plan as much as possible.
“Inventory management tools in particular allow project managers to maintain real-time visibility on the supplies and materials. If technology can help them stay within budget and estimated costs and take quick action if they see things not aligning with the plan, that’s a real and immediate benefit.”
And of course, with an eye on getting ahead of ever-tightening sustainability targets, technology that allows teams to keep track of what’s being consumed on site, will also ensure materials and supplies are used efficiently, reducing waste.
--------
This article was produced by KHL’s Content Studio, in collaboration with digital technology experts from Sortly
--------