Current affairs: Clark Rigging uses gantry system for Erie Canal lock repairs
09 October 2024
Grappling with the dual problems of an ageing infrastructure and the additional damage caused by climate change, New York State Canal Corporation has commissioned a specially-designed gantry system to carry out repairs to its historic lock gates. Lucy Barnard finds out how.
Summertime at the Waterford Flight of locks on New York State’s Erie Canal in the USA is a busy time with scores of holiday makers passing through on small boats enjoying the open countryside and spending time on the water.
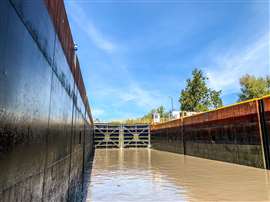
For those opening the heavy steel gates and watching torrents of water gush into each concrete chamber to change elevation and navigate up or downstream, it’s an exhilarating experience, demonstrating the effectiveness of a civil engineering project now more than a century old.
In fact, the five canal locks of the Waterford Flight in Saratoga County, New York, between them provide a total lift of about 170 feet (52 metres) in just over a mile (1.62 km) – that’s the highest lift in the shortest span in the world and greater than the lift of the entire Panama Canal.
But, for the canal’s owner, New York State Canal Corporation, maintaining and repairing the heavy lock gates – these days made from hard wearing steel instead of wood – can be an expensive and difficult process.
Like thousands of owners of historic canals around the world, grappling with the dual problems of an ageing infrastructure and the additional damage caused by climate change, the corporation was looking for a cost effective, repeatable way to carry out lock gate repairs.
During the winter season of 2023, when the corporation routinely drains this part of the canal, the corporation found that the lower gates of Lock E4, which has a vertical lift of roughly 35 feet (10.7 metres), were in urgent need of repair.
But, with each 60-foot high, 25-foot wide and 4-foot deep (18.3 x 7.6 x 1.2 metres) gate weighing 125,000 pounds (57 tonnes) each and with little space (or budget) to set up a large crane on the tow path, the maintenance team had to think of other ways to carry out the work.
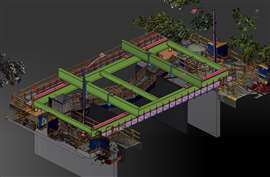
Headquartered in Lockport NY along the Erie Canal, crane specialist Clark Rigging and Rental has an annual contract for all crane and rigging services across the NYS Canal system.
“At this site, our closest crane access was over 150 feet [46 metres] radius, which would have required a large crane outside of Clark’s current fleet,” says Shawn Foti, project manager at Clark Rigging. “The costs to subcontract a large crane were not acceptable to our client.”
Instead, Clark decided to design and build a specialist gantry system specifically made for canal lock gate repairs which could be used on multiple occasions on locks along the canal.
“We proposed designing, engineering, fabricating, and implementing an overhead gantry system which could hoist both gates off of their hinges, shift inward of the lock chamber, stabilize in the vertical position, and allow for critical maintenance to be safely performed on the gates,” says Foti. “This work had been performed in the past but not with dedicated structural components designed, and more importantly engineered, specifically for canal gate projects.”
During the Spring of 2023, many site meetings were held at Lock E4 between Canal Corp maintenance supervisors, engineers, and Clark Rigging project managers. Once a conceptual plan was agreed, Clark Rigging contracted JPW Structural Contracting for the final design, engineering, and fabrication of the gantry system.
Engineering analysis and shop drawings were submitted to Canal Corp engineers and field staff for approval. Fabrication of the system was completed in October and mobilised to the site in November.
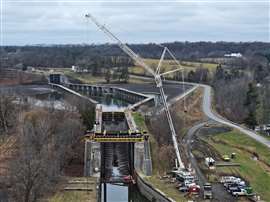
On 27 November 2023, Clark used its 400 US ton Demag all terrain crane with luffing jib to assemble the gantry system over top of the gates. Both gates were raised 2 feet (600 mm) off of their hinges and then slid inward of the lock chamber using a hydraulic jack and slide system which was installed on top flange of the large gantry header beams. Once the gates were moved 15 feet (4.6 metres) inward from the wall, they were secured down on crib piles and guy cabled off to the chamber walls for additional safety supports.
Foti says that the project, which included roughly 300 hours of engineering and project management, 400 hours of fabrication, 100 hours of crane time, and 400 hours of rigging personnel, was completed ahead of schedule and under anticipated budget, costing the corporation US$ 351,240 as the work fell outside the scope of its annual contract. Additional crane work was performed for the gate rehabilitation costing another $125,460.
He adds that the Canal Corp has already begun planning on using the gantry system at the next lock upstream, Lock E5.
“This reiterates our hard work has paid off and provided solutions-based support to a customer’s needs and budget,” he says.