Hauling solutions evolve alongside wind energy market
10 July 2023
Wind component-specific trailers create a safe and efficient solution.
In the early days of wind farm development in North America, transportation companies had to figure out how to safely haul wind components on their existing trailer fleets. As this market grew, and the components used in wind towers got longer, taller and heavier, trailer manufacturers responded with wind-specific trailers. Trailer OEMs were careful to develop products that could be adapted for other usages as well.
“In the early 2000s Trail King identified an emerging market need – trailers to transport wind turbine blades,” explained Ty Hanten, vice president of sales and marketing for Trail King. “The Trail King ‘EFX’ Extendable Blade Hauler was born. With a capacity of 70,000 pounds and the ability to haul two blades at once, the EFX was the proverbial game changer the wind energy industry needed.”
Trail King also offers Schnable systems for hauling wind tower sections, Hanten said.
“These products go hand in hand together to create a complete solution,” he said.
The market for trailers that are specifically designed for hauling wind components is constantly evolving, Hanten said.
“To keep up with the growing demands of the wind energy market, Trail King continues to develop new designs that push the envelope of blade hauling,” he said. “The company is actively working with customers to continually innovate and provide solutions for the wind energy sector by adding options for longer length and variation in holding the blade for transport.”
Ideal solutions
While transport companies don’t absolutely have to use a wind-specific designed trailer, they are an ideal solution.
“The EFX Extendable trailer is designed to accommodate a variety of wind turbine blade sizes, styles and lengths,” said Hanten. “Its narrow, double-telescopic, mono-frame main and low-profile gooseneck keep the overall dimensions to a minimum. Today’s extra-long blades can be maneuvered while in transit or at the jobsite with hydraulic turntable-style steering.”
Trail King also offers front and rear Schnable goosenecks engineered to be lightweight while still increasing payload. This product offers more lifting power enabled by operating at a lower hydraulic pressure, Hanten said.
“The supportive truss brace at the top of the tower offers greater stability and service life, and the dual-side controls are accessible from the ground level for user-friendly operation,” he said.
Early leaders
Goldhofer has also been in the wind industry since the start of the new millennium, said Jean-Philippe Martin, director of international business for Goldhofer Transport Technology.
“With the start of construction of the first major wind farms at the turn of the millennium, the first wind turbine components were already being transported on Goldhofer transport vehicles,” he said. “A few years later, special vehicles were developed for the transport of wind turbines, such as tower adapters or a blade transport device.”
In 2009, Goldhofer developed a transport system to pick up and transport the 2 MW nacelle (V112) from Vestas. In 2010, Goldhofer presented a new concept for the transport of individual wind turbine components such as rotor blades, hubs, drive trains, nacelles and tower components.
“Transporting vehicles for the wind energy industry have become an important part of the industry,” said Martin. “Especially in the context of the expansion of alternative energies due to climate change, flexible and innovative solutions are required to transport the ever-growing number of wind turbine components to the windy regions of the world in an environmentally friendly manner. This is where Goldhofer comes in with its innovative vehicle technology, such as the FTV 850 blade carrier presented at Bauma22.”
The advantage of these specially designed trailers is that these vehicles use fewer resources and are more sustainable, saving the operator time and money.
“The modular design of the vehicles means that they can be used for other types of transport, allowing users to operate their fleets economically,” Martin said.
Paul Hönen, Faymonville’s sales manager for North America, said wind power projects include many specialized transportation tasks when it comes to installing and maintaining windmills. With telescopic single-drops, double drops, extendable stretch single-drop trailers as well as self-propelled vehicles from the Faymonville Group, all components of a wind farm can be moved in a time- and cost-effective manner.
Hönen said the Faymonville range is completed by special equipment such as the blade lifter for the transport of wind turbine blades and tower adapters for super heavy applications.
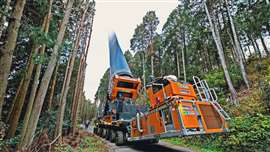
“Within the Faymonville Group, the development of specific solutions for the wind industry has always been a priority,” Hönen said. “The market and especially its challenges are rising during the last years. The plants become bigger for more efficiency, the blades longer and the elements heavier, higher and larger. The Faymonville Group has developed new products to solve these missions.”
One of the latest product developments is the BladeMAX1000 by Cometto, Hönen said.
“The BladeMAX1000 with its 1,000-metric-ton load capacity is the most powerful available on the market of blade lifters,” he said. “This equipment has two movement axis – rotor blades are raised up to 60 degrees and can also be rotated by 360 degrees. Greater handling stability is guaranteed by the similarly patented stability control system.”
Safety sensors
Hönen said the data from diverse sensors on the BladeMAX1000 are collected and sent to the central control unit, which processes them. All safety-relevant information is constantly monitored. The operator receives a signal as soon as critical values are approached. The tolerance is larger than other systems he said. The interaction of electronics, hydraulics and visualization increases the safety during the shift of the center of gravity when moving the blades.
Low bed vehicles are generally used to transport hubs, nacelles and tower segments to the jobsite, he said.
“This vehicle type makes it possible to cope with underpasses, despite the high load,” Hönen said. “Whether for long tower segments or heavy nacelle elements, single drop trailers are variably adaptable and thus versatile in use. For projects in the wind power sector, the easily maintained all-rounders from Faymonville are economical and future-oriented. Simple, but carefully conceived technology is combined with a light and sturdy design.”
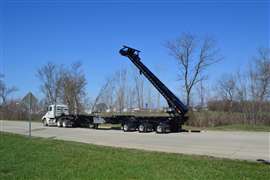
Rotor blades are fragile because they are made of lightweight glass fiber-reinforced plastic. The TeleMAX product series meets requirements for the economical transport of long and very fragile elements, Hönen said.
XL Specialized Trailers first entered the wind industry with a trailer solution in 2009, according to Tim McGreal, director of engineering.
“At XL, we have trailers specifically designed to transport the each of the various parts of a wind turbine,” McGreal said. “The Lightweight 14 axle is a perfect solution for hauling the nacelle, the Blademate or Schnabel and Dolly system to haul blades, and the Towermate to move the towers. XL is known for designing trailers specific to the customer’s loads, and our trailers for the wind energy market are a great example of that.”
Customized solutions
McGreal said that for safety, XL’s Blademate trailer has forward and rearward facing LED indicators, letting drivers know if the power unit is on or off. It was designed with a mechanical steering lock that prevents inadvertent steering.
“It also has a 48-inch-wide rolling load bolster and a 20-foot pullout bumper that can be moved by hand without the need for additional equipment,” he said. “XL’s Blademate utilizes a double roller design to eliminate friction and allow the trailer to extend and contract smoothly.”