How DST and Tagregados demolished the Gouvães Quarry
11 June 2024
D&Ri speaks with DST (Domingos da Silva Teixeira) and Tagregados, both part of DST Group, about its recent demolition and remediation of the Gouvães Quarry in Portugal.
Nestled away in Northern Portugal, there is a beautiful, green ‘lakeland’ habitat within the protected, 600-sq km Alvão/Marão Natura 2000 site, that looks as if it has always been there.
But in fact, it is a reservoir – the Gouvães Dam Reservoir, and it has only been there for a year, having been created by the construction of the Gouvães Dam and the demolition and remediation of the Gouvães Quarry.
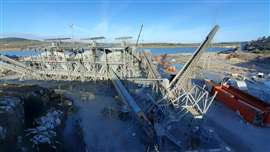
About Gouvães Quarry
The quarry was built specifically to enable energy giant Iberdrola to construct three hydroelectric dams on the Tâmega and Torno rivers, within the Douro river basin, which would collectively generate 6% of the country’s energy needs.
As such, its construction, operation and eventual decommissioning of the quarry facilities were all subject to heavy environmental regulation.
Strict oversight from the Portuguese Authorities, DGEG (General Direction of Energy and Geology), APA (Portuguese Environmental Agency), the ICNF (Institute for the Conservation of Nature and Forests) and the CCDR-N (Commission for the coordination and development of the Northern region) were central to the project from the very beginning.
At the end of the quarry’s eight-year working life – by which time it had produced aggregates for the three hydroelectric dams, a complex deconstruction procedure was undertaken to apply the environmental restoration plan approved by the permitting authority.
As such, its construction, operation and decommissioning were all subject to strict regulation and oversight from Portugal’s Directorate General of Energy and Geology (DGEG), the Portuguese Environmental Agency (APA), the Institute for the Conservation of Nature and Forests (ICNF), and the Commission for the Coordination and Development of the Northern Region (CCDR-N), from the very beginning.
At the end of the quarry’s eight-year working life, a complex deconstruction procedure was undertaken to apply the approved environmental restoration plan.
Scope of Works
The 27-havquarry site comprised an 8-ha crushing plant incorporating ten screens, one jaw crusher, two cone crushers, a vertical shaft crusher, 1.5 km of conveyor belts, and six storage silos.
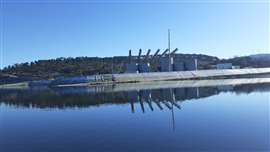
Two sides of the quarry’s plant were surrounded by a giant cofferdam made of HDPE (high-density polyethylene) film, two layers of geotextile, soil and a rockfill retaining wall to protect the quarry from the reservoir’s waters.
While DST’s main scope of works had been constructing the quarry facilities and producing the aggregates for the construction of the hydroelectric dams, they were also responsible for closing the quarry at the end of the infrastructure project.
Thus, the clearing and restoration of the site presented a unique set of challenges for main contractor DST.
Chief among these challenges was having to complete the works within just a three-month timeframe. To achieve this, DST determined to carry out the demolition and remediation in two distinct phases.
The first phase would see the complete removal of all facilities, equipment, plant and structures on the site, with the land restoration works also undertaken in the same period.
Then, following reservoir testing by Iberdrola, the second phase would comprise the removal of the cofferdam – the final manmade structure on the site.
Clearing quarrying site
DST began the first phase of the project by dividing the site into four distinct zones, so that it could remove the silos and clear the plant, equipment, infrastructure and support facilities, concurrently.
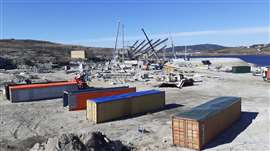
Nuno Faria, Project Manager at DST Group, says: “All the steel from the plant had to be carefully dismantled, as it was to be transported to Angola for use on another quarrying site.
“In total, the plant and equipment filled 150, 40-ft shipping containers. So, it was quite a logistical challenge.”
Heavy lifting: dismantling giant structures
A key part of this first phase of the demolition project was the dismantling of the site’s six silos, which had been used for the storage of 12,000 t of aggregates.
Measuring 30 m high, with base diameters ranging from 9 to 11 m, the silos sat on top of a reinforced concrete slab.
“Each silo comprised of twelve metal rings, measuring 2 m in height. Each ring layer had several steel plates that were bolted to each other and to the next ring,” says Nuno. “So, for the assembly of the silos, we used a crane, to test how best to assemble them.
“First, we tried to erect a silo piece by piece, one ring at a time. And at the time, we thought that this would also be the easy way to dismantle the silos.
“However, we quickly realized that this could deform the shape of the metal rings.
“And as the silos, along with all the other plant and equipment were due to be transferred to another site and used again, this was not something that we could risk.”
Nuno says: “Additionally, taking them apart piece by piece would not have been possible within the three-month timeframe we had for the demolition.”
In the end, DST assembled each silo directly on top of the slab, again one ring at a time, but only up to half their total height.
While this was being done, a second team assembled the top half of each silo on the ground, which was then lifted onto the base half of the silo that was already on the slab.
“This gave us some real clues as to how we could accelerate the dismantling job later,” says Nuno.
“Taking into account the maximum load capacities of the crane, we decided to take the silos down – not in two sections, but in three sections. With each section comprising about four ring layers.”
Nuno adds that because the silos, by this point, had been in use for almost eight years, their structural integrity was also a key consideration during the deconstruction.
“We didn’t know how the wear of the silos had affected their structure. So, when we needed to remove them, we had to be extra careful.”
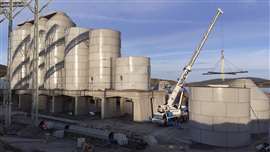
“To solve the problem of deforming the structures, we designed a supporting cross-brace that was attached to the crane,” Nuno explains.
“The design allowed it to be attached to the silos’ ring layers via four fixation points, accommodating the 9, 9.5 and 11-m diameters of the silos.
“The cross-brace was very important for both distributing the load and for preventing the ring-shape of the silo layers from distorting.
“Yes, we lost some time preparing it and studying it, but it also really accelerated the speed at which we were able to bring the structures down.
“And this was critical to enabling us to complete the work within the short three-month window that we had, because we knew that demolishing the slab - on which the silos had been sat, would take a lot of time.
“So, developing the cross-brace proved to be a real game-changer.”
It took a DST taskforce of 20 demolition workers, using two telescopic cranes, four lifting platforms, a backhoe loader, two forklifts and a crane truck, to complete the dismantling.
Removing reinforced concrete structures
With the silos removed, DST Group’s specialist demolition, blasting and drilling division, Tagregados, could then demolish the concrete slab, on which they had been sat.
But by this time the specialist contractor had just two weeks in which to complete the task, and in the end, it proved to be one of the project’s most difficult undertakings.
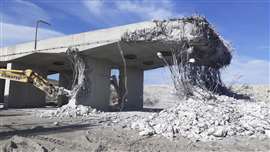
“When you look at the photographs, it looks small. But it was not small,” says Diogo Fonseca, General Manager of Tagregados.
In fact, the slab measured 60 m long by 12 m wide and 1.5 m at its thickest points – with over 350 t of steel and around 1,200 cu m of concrete contained in the upper section alone.
“We did study different solutions before starting the demolition, including diamond wire cutting. But we didn’t know how the diamond wire would cope with that much steel, and we determined that it would also take too long to do,” explains Diogo.
“We also explored the use of explosives to create key cuts to lower the structure. But again, with the amount of steel inside the slab, this didn’t give us a good level of comfort to be certain of the result.
“To get the slab demolished in the two weeks we had, the only real option was to mechanically bring it down.”
Thus, Tagregados deployed six 36-t hydraulic excavators, two 24-t hydraulic excavators, a mobile jaw crusher and numerous hydraulic hammers, multiprocessors, and pulverisers for the task.
“The upper slab was held up by multiple sets of pillars, which supported arch-roofed sections.
“At its thickest point it was 1.5 m thick and at its narrowest points it was 1 m thick, and so we initially thought that if we removed the first pillars, that this would be the breaking point,” says Diogo.
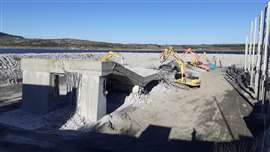
“But of course, because it had been designed to carry the 30-m silos - and the 12,000 t of aggregates inside, the structure was so strong that when we removed the first pillars, the upper slab didn’t move. It was still there. Because at its narrowest, 1-m-thick points, it had been reinforced with three layers of 32-mm rebar.
“So, when we removed the first pillars, nothing happened. Only when we removed the second set of pillars, did we achieve the breaking point on the next arch-roof section at its narrowest 1-m point.
“And this pattern of breaking was repeated in every second section of the slab. So, it certainly proved that it was well-built. It was bullet-proof.”
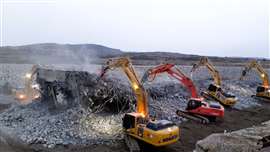
After a repetitive cycle of hammering, shearing, pulverizing and crushing, for which the process took up nearly 3-ha of space, the separated steel and concrete were sent for recycling.
According to Diogo, demolition of the structure and the removal of the resulting debris was completed in just 12 days – well within the allotted two-week timeframe.
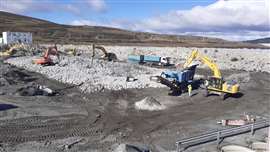
Dismantling a cofferdam
The successful slab demolition and the subsequent opening of the cofferdam (for safety reasons), signalled the end of the first phase of the demolition and restoration project.
And, following a three-month window of time in which Iberdrola carried out its testing of the newly-created Gouvães Dam Reservoir, DST, began the final stage of the project; dismantling the giant cofferdam that had protected the quarry site from the reservoir’s waters.
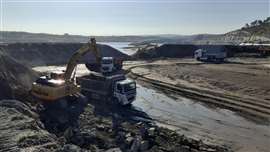
“When we resumed work on site, we again had only two weeks to remove the cofferdam,” says Nuno.
“And because the reservoir was now operational, the water level was rising and falling to certain levels.”
The cofferdam measured over 0.5-km long and 5-m high, with a base up to 30 m wide and a top width of 6 m.
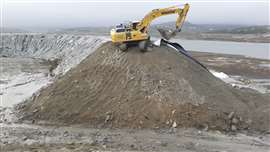
It comprised soil, a rockfill retaining wall, two layers of geotextile (1,200 and 300 gr) with an impermeable HDPE film in between, which protected the outer side (water side) of the structure.
Once the level of the reservoir reached its lowest level, the massive earthmoving process began and, in the end, the cofferdam was completely taken down two days ahead of schedule.
When the entire hydroelectric dam project was complete, this section of the once narrow Torno River had been transformed into a working reservoir lake, that when at its peak water level would cover the majority of the Gouvães Quarry site.
“In a few more years, you will see the entire area covered with vegetation. Trees, bushes, grasslands and the water is all you will be able to see,” Nuno concludes.
The Quarry won the European Sustainable Development Award, promoted by UEPG.
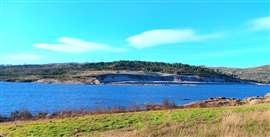