How gantries are revolutionizing infrastructure projects across the U.S.
05 August 2024
When it comes to thinking outside of the box for unique rigging solutions, gantry systems are often an adaptable alternative to huge and expensive conventional cranes. Utilized at both indoor and outdoor jobs, gantries are a portable and popular solution in the rigging and specialized lifting realm. These simple yet mighty machines can be deployed to a jobsite and get right to work.
Hoisting reactor vessels in California, setting a generator, modernizing a Chicago Transit Authority rail line and restoring an historic canal, American Cranes & Transport has compiled several interesting projects that were performed using gantries.
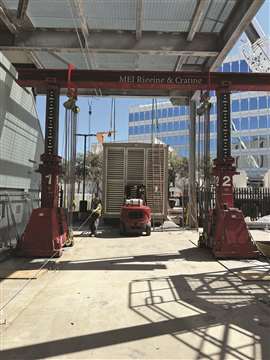
Skates and tanks
MEI Rigging & Crating was brought onto a complex data center project site to set a generator in a limited working space. Due to the tight clearances and the exact setting of the generator, weeks of measurements, calculations and critical design decisions were made by the MEI team. It took every inch of space from overhead room, gantry set up and even the MEI platform to make the plan work.
The MEI team offloaded and set the 50-foot by 12-foot subframe onto an MEI platform, then rigged and secured the generator onto it. The crew rigged and set the enclosure and married together all three pieces to be moved as one, weighing 126,000 pounds. Using eight trail skates along with winches, the team skated the assembled generator under the customer’s steel structure. Once in place, the team then rigged the three-piece generator to the 250-ton gantry set using the eight, 10-ton chain hoists. MEI then hoisted the generator within ¼-inch of the overhead steel structure and placed maroon blocks under for safeties. The next step was to rig, offload and pin roll two 25-foot-long by 12-foot-wide steel tanks (25,000 pounds each) using the MEI platform, one-inch pin rollers and winches. The MEI team carefully pin rolled each tank under the generator with only ½-inch of clearance between the tank stub ups and the bottom of the subframe.
Once both tanks were set in place and married together, the team then used the 250-ton gantry to carefully lower the generator onto the tanks making sure all bolt holes, exhaust and fuel lines lined up and married together.
Component configuration
Bragg Companies was contracted to offload, transport and store four reactor vessels from Pier F in Long Beach, CA to Bragg Companies’ headquarters. The four reactor vessels varied in weight from 280 to 583-kips. This process required a series of transloading and staging operations carried out by the company’s core divisions.
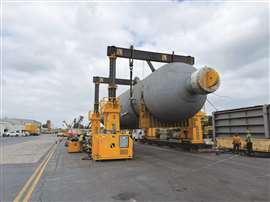
The J&R Engineering 700-ton model T1402-4-39 gantry was used to transfer the vessels to the Long Beach yard for final staging and storage. The gantry’s hydraulic pump unit is operated by diesel motor or 480V 3-phase power. Each vessel was lifted and held 60 inches above the ground before positioned within the gantry footprint. The crew performed a required five-minute lift and hold during each transload.
The header beams for this lift, designed by Bragg’s in-house engineering department, featured a modular design with seven components that can be configured in five different lengths, ranging from 30 to 120 feet.
Quick turnaround
Redding, CA-based CalPortland Cement found themselves in an unenviable place in the spring of 2024. One of their ball mills required a head replacement – immediately. Time was of the essence. The plant staff reached out to Machine Repair International – commonly known as Vezers Industrial Professionals.
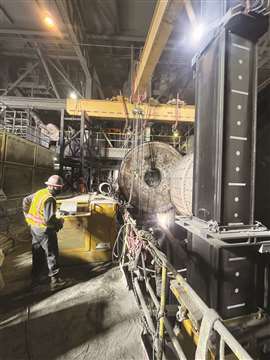
With only weeks’ notice, Vezers was on the job. And this job presented many challenges. The plant layout had extremely tight quarters. The mill head was sandwiched in between a low overhead structure limiting lifts to inches. Surrounding the mill was a small opening just inches larger than the width of the head. And below the mill, there were supports that restricted the head’s exit in and out the building. The team raced against the clock as CalPortland needed the head replacement immediately. Vezers was also tasked with designing and constructing all other support structures necessary to remove the head.
The company’s in-house engineering staff designed a twin support system supplied by Rigging Gear Sales. RGS supplied and transported a lift system with a Model 34FBG5400WTI - 500T Power Tower, two 40-foot Box Girder Header Beams, a 400-ton Powered Side Shifts with Adjustable Lift Links, four 10-foot sections of 20-inch Runway Track, numerous Track Elevation Stands and several highly qualified operators, cross country, within a 10-day window. The erection was completed in a day.
Locked and loaded
Clark Rigging and Rental is headquartered in Lockport, NY along the famous Erie Canal and has an annual contract for all crane and rigging services across the NYS Canal system. This year, the team’s project included developing a design/build rigging plan to service the Lower Lock Gates at Lock E4 in Waterford NY.
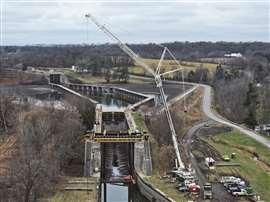
Lock E4 has a vertical lift of roughly 35 feet, which means the water differential from the upper chamber to the lower chamber changes 35 feet when a boat is navigating the lock. Large steel gates are used as doors to close the chamber and then a pump adjusts the water heights so boats can safely change elevation to travel upstream or downstream. The lower gates at Lock E4 are 25 feet wide, 60 feet high, 4 feet deep and weigh 125,000 pounds each.
Clark proposed designing, engineering, fabricating and implementing an overhead gantry system which could hoist both gates off of their hinges, shift inward of the lock chamber, stabilize in the vertical position and allow for critical maintenance to be safely performed on the gates.
A critical component
Fagioli was involved in the transportation and installation of a new baggage handling system at Houston’s International Airport.
Fagioli transported a bridge from the manufacturing area by SPMTs and lattice tower and moved it to the installation area. At the end of the bridge, Fagioli connected lifting beams provided with four strand jacks (50-ton capacity each) which would be then used for the final lifting activity. It was necessary to use additional support plates at the extremes of the beams so the fixed anchors and strand jacks could fit properly on the structural beams.
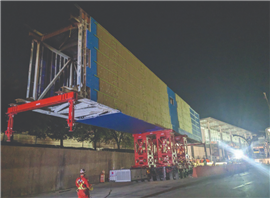
Fagioli planned three nights for road closures. On the first, SPMTs moved the bridge in less than 30 minutes. On the second, Fagioli prepared an additional 6 axle lines SPMT positioned onto 120 timber crane mats. The SPMTs positioned in the center were removed and the set positioned at the back started maneuvering to align the bridge for the final lifting operation. The bridge was hydraulically lifted to the designed height. The bridge was then connected to the strand jacking system positioned at the extremes of the beams under the heavy item. The strand jacking system lifted the bridge. On the last night, the bridge was lifted to its final elevation.
Riverside rigging
Oxbo Mega Transport Solutions was appointed by JH Kelly Industrial Contractors with the lifting/rigging, transportation and installation of a newly fabricated gallery conveyor measuring 314 feet long, 12 feet wide, 16 feet tall and weighing nearly 250 tons. The project was located along the Oregon/Washington lower Columbia River in December 2023.
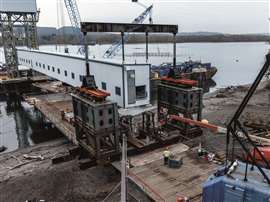
At the fabrication facility, the Oxbo team elevated the structure 15 feet to prepare the unit for the installation of the fabricated steel fixtures. The crew utilized SPMTs to lift the galley and followed up with a blocking system. The conveyor was remotely driven onto a barge using 28 lines of Oxbo’s Goldhofer PST/SLE modules. The crew needed to maneuver the gallery from the offshore barge between two fixed towers with less than 6 inches of clearance. Then, the onshore end of the gallery was passed to a 300-ton derrick crane to assist in positioning atop a work bridge.
The onshore end of the gallery was required to be lifted approximately 24 feet above an already elevated foundation built into the side of the approach to the river. This final elevation would allow the permanent “kickstand” to be installed.
Heavy transverse beams were installed atop the foundation to support Oxbo’s modular truss system. The 400-ton gallery was then lifted 10 feet using the 400-ton gantry in a long rigging configuration so it could be temporarily supported and re-rigged.
Let’s talk transit
Mi-Jack’s MJ55HD Travelift is playing a pivotal role in Chicago’s Red & Purple Line Modernization (RPM) Program, the largest capital project in the history of the Chicago Transit Authority (CTA). Partnering with the Walsh-Fluor Design-Build Team, Mi-Jack’s MJ55HD is tasked with efficiently positioning concrete segments into the existing infrastructure, which is critical to the project’s success.
Designed specifically for urban construction environments, this particular MJ55HD’s compact size allows it to operate beneath a launching crane, navigating narrow spaces with ease. This capability is essential in maximizing efficiency and minimizing disruption to both workers and commuters. Its speed and safety features further enhance its suitability for high-traffic areas, ensuring that construction activities proceed smoothly without compromising safety standards.