Innovation and acceleration: Quick-turnaround projects by SC&RA members
18 May 2023
In recent years, Accelerated Bridge Construction (ABC) technologies have changed the ways state DOTs do business. Projects can be reduced to as little as 48 to 72 hours, and the project life-cycle, from planning through construction, can be trimmed by years.
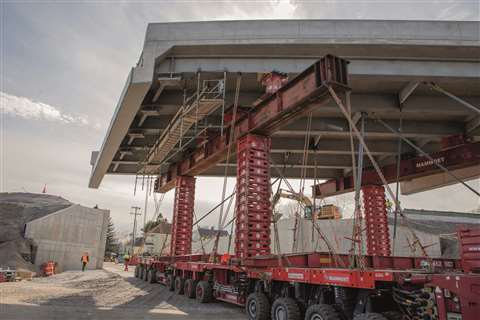
Accelerated project times significantly reduce traffic delays and road closures, danger to both workers and the traveling public and can potentially reduce project costs as well. Additionally, state-of-the-art ABC planning and construction methods, designs and materials are producing safer, more durable bridges with longer service lives than conventional bridges.
A recent example of such work involved SC&RA member Mammoet on a project planned and executed by MaineDOT that saw a bridge carrying I-295 over Veranda Street in Portland (Maine) replaced in a weekend back in April 2022.
Per MaineDOT, the use of conventional construction methods would have stretched the endeavor to at least four years and involved building a temporary bridge, closing related off-ramps and potentially demolishing nearby buildings – all of which still didn’t factor in daily traffic jams for the 55,000+ motorists traveling the route each day.
MaineDOT teamed up with American infrastructure design firm HNTB Corporation, and reimagined the project using ABC methodologies. The result was the removal of the 60-year-old structurally deficient I-295 bridge and the insertion of the replacement bridge and related infrastructure – including paving, striping and re-opening it all to traffic – in less than 72 hours.
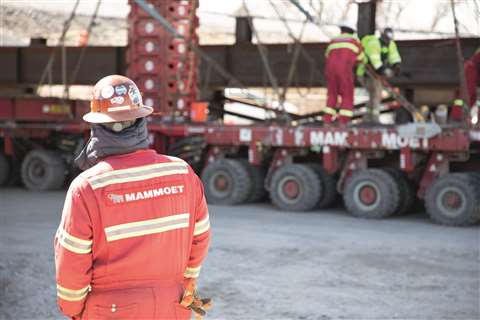
“Typically for a project like this, we gather the plans from the client and have them supply us with the weights and specs for the bridge structure to be moved,” said Mammoet Project Manager Matt Boben, who worked with contractor Cianbro on the project. “Then, we go to what we call our toolbox and see what equipment we have that is suitable for the job.”
In this case, Boben and his team opted to employ Mammoet’s innovative Mega Jack 300 SPMT cradle system to jack up each of the bridge spans to the required elevation, which was approximately 7.6 meters (25 feet) high. Cianbro’s solution ultimately involved building the upper portion of the new bridge to the side of the existing one on temporary supports – a method that normally requires both lifting equipment and falsework to successfully set the bridge. But Mammoet’s cradle system essentially allowed for the bridge to be rolled into place, which not only reduced steel mobilization and trimmed more than two hours off the installation, but created an opportunity for the bridge to be built closer to the ground and farther from active traffic, enhancing safety for team members and motorists.
“We were able to come in five days prior, jack up both bridges and then drive them into position one at a time,” added Boben. “Because of the jacks, we were able to come straight down and set everything where we wanted to right away.”
Boben only sees more projects taking shape like this one as infrastructure needs across the country only increase. “While this type of work has been going on for years, innovating on some of the equipment like the jacks and the SPMTs is creating greater efficiencies and you tend to be able to accelerate things more quickly. At the end of the day, roads are only getting busier, traffic is only increasing and various types of infrastructure – especially bridges – are deteriorating more rapidly. So, doing work in this way – off to the side while traffic keeps moving – is definitely the future.”
Within one shift
Jerry Rothwell, director of Sales for North America/Transport Technology at SC&RA member Goldhofer, appreciates the ingenuity that companies today are putting into practice to come up with solutions for projects that are literally changing the game.
“If you have the geography to do so – you can put together SPMT pieces and go as big or small as you need to do to get a job done – whether they’re joined together or in a free arranged combination,” he said. “Combining them with the jacking systems has created some innovations that just blow my mind – and I think this type of technology lends itself very well to projects like rapid-bridge replacement, among others.”
Like Mammoet, another SC&RA member company that utilizes Goldhofer equipment is Louisiana-based Berard Transportation – who completed an ABC project as recently as March 2023 by changing out a damaged bridge section on Interstate 10 in Lafayette, LA.
“An over-height load impacted the bridge in early January 2023, and on January 20, we removed the damaged girders,” indicated Brett Berard, vice president of operations. “This is a major intersection of heavily traveled I-10. The girders were on an exit lane, but they were damaged so badly that the dead load of the girders was being held up by the girders in another lane. So they had to get the dead weight of those two damaged girders off – in order to open up both travel lanes. The same weekend that we were able to remove the two damaged girders, they were able to open two travel lanes of I-10. For context, when it was down to one lane, they had traffic backed up to about seven miles.”
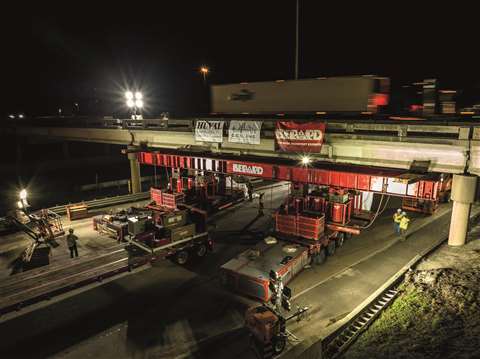
In the two months or so between the project’s beginning and Berard’s placement of the new bridge section, the contractor built the section off to the side in a laydown yard just a few hundred yards away.
“And so, on March 17, they did another complete closure of I-49 below, and we installed the new section that evening,” Berard confirmed. “By 7 a.m., we removed a third damaged girder with a crane and then installed the new three-girder section all within one night shift.”
Quick turnaround
To get the job done, Berard ultimately utilized two six-line Goldhofer PST/SL-E transporters.
“We also used eight climbing jacks on top of steel support stands controlled by a Jahns Structure unified jacking system,” added Berard, “and we had a seventy-five-foot or so custom-built girder beam that was able to support the bridge span to DOT speck. They did their continuous monitoring of the bridge and stresses on it during the move, and they had no issues.”
As for the unique aspect of the job, Berard noted, “Obviously, the quick turnaround was unique, and we’d done a similar project before this, so we had a similar gameplan, but what might have been the most unique part for all of us is that everyone slept at home. It was a hometown project for us.”

That said, he established, “… the precision and capability of this equipment we use creates the most prevalent way to do projects like this. Sure, we could get big cranes out there, but we’re able to put all of our lifting equipment on the SPMTs – all the jacks, the cribbing, everything on the transporter deck – so it makes it really efficient from the time they close the interstate until the time they open it.”
And since jobs like these are a bit of a break from the norm, explained Berard, it was good for the company to work within the additional challenge.
“It might be a little intimidating to be in the public eye on a project like this – and you want to make sure you don’t waste the opportunity and become a negative aspect to the job. But you ultimately just have to use your experience and make sure it goes well.
“As far as the ingenuity, if we stick by the methods we did decades ago, the industry would only suffer. So when we see something that’s impressive and has some ingenuity behind it, it helps to replicate it if and when possible. All the more reason to spotlight projects like this one, and the many others like it.”