Monumental moves: inside some of 2024’s complex rigging and transport operations
28 October 2024
Edwards Moving & Rigging (EMR) recently completed a monumental transport and rigging project that required some extra specialized rigging expertise. For a sensitive decommissioning project, EMR successfully moved four Class 7 radioactive components from Florida to a disposal site in Texas. This intricate operation, requiring months of planning, involved multimodal logistics, sophisticated rigging and precise coordination across numerous state agencies and infrastructure.
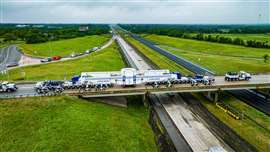
The first phase involved transporting the components from a staging area in Florida to a barge landing site. EMR utilized a 3-file, 12-line Goldhofer PST to roll the four components – two smaller units and two larger ones – onto a 50-foot wide by 200-foot long deck barge. The two smaller units were secured on stands and beams, while the larger components were staged using EMR’s low-bearing pressure system, designed to distribute component weights evenly. This enabled all four units to be loaded onto a single barge.
Once secured for lateral, longitudinal and uplift movements, the barge traversed the Gulf of Mexico, arriving at Rockport Terminal in Aransas Pass, Texas. The entire process was then reversed as EMR employed a RORO technique to offload the cargo.
Months before the barge set sail, EMR began an intensive route planning process with TXDOT and third-party bridge engineers. Given the sheer weight and size of the transport – culminating in a gross vehicle weight of 1,553,344 pounds at 300 feet long, 21 feet 5 inches wide and 17 feet 2 inches tall. It was crucial to ensure that roads and bridges could support the extremely heavy load.
The planning process took eight months, involving 11 of Texas’ 25 transportation districts. Each district posed its own challenges, with several requiring road closures, rerouting of traffic and traffic control plans. EMR’s rigorous analysis ensured that the transport could proceed without damage to infrastructure or disruption to the public.
Once the permits were secured and the route was finalized, EMR began the over 900-mile road journey to the disposal site. The convoy navigated 158 bridges, utilizing dollies on 150 of them, and performing pier-to-pier jumps on three bridges. The team also managed two contraflow movements, temporarily closing sections of the interstate and moving in the opposite direction to accommodate the oversized load. At one point, a section of Interstate 20 was shut down to allow the transport to proceed.
In addition to the technical challenges, logistical hurdles such as removing 73 road signs and using bucket trucks to navigate wires and traffic lights added further complexity to the operation. Police and civilian escorts ensured public safety and clear passage through towns and rural areas alike.
One of the most notable engineering challenges involved the transport of the larger radioactive components using the Goldhofer Faktor 5 high girder bridge system. The components didn’t have traditional lashing points, which are typically required for securing cargo during transport. Edwards’ engineering team devised a solution using synthetic chains to wrap and secure the cargo in compliance with TXDOT standards.
Upon reaching the disposal site, the components were transported the final mile using a 3-file 12-line Goldhofer and a 900-ton gantry system, which offloaded and set the components to the ground.
Setting an ONA press
Taylor Crane & Rigging supplied supervision, manpower and equipment to offload and rough set an ONA press. Equipment used on this project included two 690 ton jacks, walking beams, lifting beams, lifting links and rigging, a 40/60 Versa-Lift and a 15k Forklift.
Autoclave replacement
A manufacturing company in Arlington, WA, decided to upgrade their telephone pole pressure treating equipment – a 150-foot-long, 8-foot in diameter autoclave – with a larger system to increase its production volume. However, the 160,000-pound autoclave sat in a below-ground pit under a covered pole barn with a machinery pit directly below.
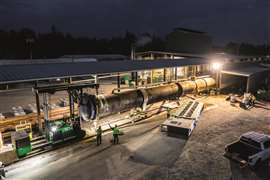
Reaching out to Omega Morgan’s Seattle machinery moving team, the company needed a full-service solution to remove the original vessel, transport the new autoclave and install it within the current location – all while minimizing production downtime. Omega Morgan’s crews stepped up to the plate with a world-class solution.
Months ahead of the move, the machinery moving crew sought support from Omega Morgan’s specialized transportation and crane services teams. They would be integral to the pickup and transport of the new 230,000-pound autoclave from Sandy, Oregon.
The specialized transport team began applying for super load permits from both Oregon and Washington State authorities – which take between 45 and 60 days – while the machinery moving crew planned the multi-stage move.
Though it would maintain a 150-foot length, the new autoclave added two additional feet in diameter to be placed in the same space as the original vessel. Over the course of several meetings and site visits to the Arlington site and Sandy manufacturing facility, the team discussed changes to the design of the new 230,000-pound autoclave and determined the equipment necessary for the removal and installation moves.
After getting permits, Omega Morgan’s specialized transportation team turned to the transport segment of the project. They decided on using a custom Omega Morgan-built modular dual trailer set up for the haul between Sandy and Arlington.
The project was timed between departments to ensure the least amount of production downtime for the client. Once the permits, equipment and crews were ready, the machinery moving team executed the first stage of the project.
Over the course of three days at the Arlington facility, Omega Morgan’s four-person crew used jacks to lift the autoclave before skating it out and over the pads that supported its base. More jacking and cribbing brought it high enough to clear the pit, yet remain below the roof. The crew then used the Tri-lifter to pull it out the rest of the way. Sliding a SPMT under the vessel, it was moved away from the pit for decommissioning.
The next segment of the job began in Sandy, OR. The specialized transportation team of four met the crane crew and 200-ton and 350-ton cranes at the autoclave manufacturing facility. Lifting the new, 10-foot in diameter autoclave off its blocks, the crane services team placed the component between the two custom-built modular trailers, connecting them. After lashing the autoclave in, the team got on the road. With road closures, traffic control and pilot escorts, the 18-foot wide load made the journey in three days.
Back in Arlington, the installation crew lifted the autoclave off using Tri-lifters before setting it on a slide track and pushing the component back toward the pit. Installation took six days as the team jacked and slid the vessel into place.
Railway bridge replacement
In July in Vermont, Buckingham Heavy Transport lifted and transported a 125-foot by 22-foot 6-inch single-span railway bridge from its staging area to permanent abutments. The bridge was fabricated in an adjacent lot a couple hundred feet from the abutments.
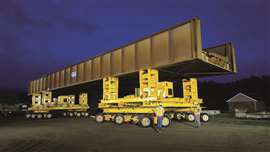
The Buckingham team lifted the 555,000-pound bridge to an elevation of 16 feet using cribbing and jacks, and then assembled custom dolly transporters made up of Buckingham power and coaster dollies, three levels of steel beams and 150-ton stands under it.
Next a Buckingham slide system was integrated between the beams to allow for lateral adjustment. The bridge systems were then driven across the lot and into position.
Buckingham’s fleet of custom equipment allowed the team to complete the bridge placement within the client’s tight time constraints. Buckingham’s dolly transporters’ crab steer capabilities allowed the team to drive the bridge section diagonally from the staging area and into alignment with the abutments without time-costly maneuvering.
The integrated slide and jacking systems enabled for the team to adjust the placement of the bridge precisely and quickly on location.
The list of equipment required was long and included Buckingham Power and Coaster Dollies, 30-ton Buckingham Crib Jacks, Buckingham 12-Port Unified Jacking Machines, Buckingham Power Units and the Buckingham Slide System.
Coil handling
At Nucor Steel Gallatin in Ghent, Kentucky, efficient material handling is crucial to maintaining smooth production processes. To meet this demand, Nucor relies on Mi-Jack Products’ 70-ton capacity rubber-tired gantry crane, outfitted with a custom coil handling attachment and a hydraulic-powered rotating hook, specifically designed for specialized lifting applications.
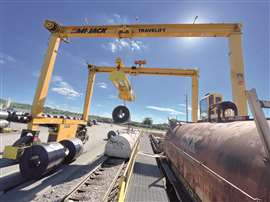
The MJ70HD Travelift Rubber Tired Gantry (RTG) crane is equipped with Mi-Jack’s specialized coil-handling attachment, which features a hydraulic-powered rotating hook engineered to
lift and rotate heavy steel coils with precision as railcars move beneath.
The design allows for the seamless loading and unloading of coils into railcars at the Gallatin facility, where over 3 million tons of hot band coils are produced annually.
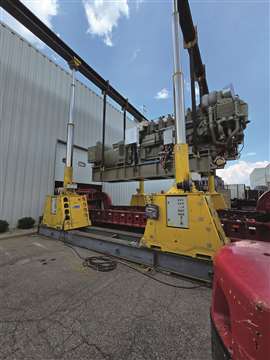
“Combining the Mi-Jack Travelift, rotating spreader bar and C-hook enhances both productivity and safety by eliminating the need for ground rigging and keeping personnel at a safe distance while coils are being hoisted
or lowered into railcars,” said Mike Lanigan, vice president of sales for Mi-Jack.
At Nucor Steel Gallatin, the Mi-Jack Travelift drastically reduces coil-handling time. The crane’s custom design allows it to work over railcars as they move along with its tailored width and height specifications. Its 70-ton capacity, coupled with the rotating hook and C-hook, allows operators to load four steel coils per railcar in under 30 minutes and is then dispatched to its next destination, ensuring a streamlined supply chain between Nucor’s steel mills and processing facilities.
Generator installations
Tri State Rigging recently moved and installed multiple 147,000 pound generator sets inside test cells using their 400-ton gantry system. Working for TRP Laboratories in Colombus, Indiana, the Tri-State team was able to relocate each generator set onto isolator pads using their battery powered Hillman Traksporter system and hydraulic toe jacks.