On the road again: First-hand look at Spain’s equipment manufacturing
04 August 2024
There’s no better way to get the feel of a market than hearing from those with their ‘boots on the ground.’
That’s exactly what a recent trip to Spain gave IRN the opportunity to do, thanks to an invitation from ANMOPYC, the Spanish manufacturers association for construction and mining equipment.
Our trip, organized by ANMOPYC in collaboration with ICEX, started with a visit to Barcelona, a hub for a number of OEMs along the ANMOPYC trail. It is here that we visit Roquet Hydraulics, which is headquartered in Tona, just outside the city.
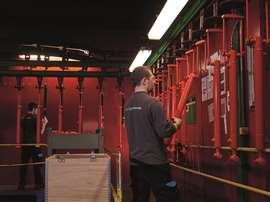
The company specializes in the design and production of gear pumps, cylinders, motors and valves for hydraulic systems used across mobile machine and agricultural applications. As part of this, the company incorporates testing facilities to determine such issues as part fatigue and corrosion resistance, while also offering advice on best manufacturing practices.
Close to the company headquarters, a plant in Centelles manufactures a broad range of cylinders for hydraulic applications. Operated under the Dinacil brand (part of the Roquet company portfolio), the parts are used in construction and agricultural machines, plus a series of other industrial applications.
All parts for the cylinders are produced in Europe by Roquet; Dinacil has a sister plant in Romania which also produces cylinders. With that in mind, it’s surprising to learn that Roquet has no current, or indeed any future plans to start production in China.
“We hear that question all the time at trade shows, ‘do you make the parts in China?’” says Ruth Martinez, from the sales and marketing department.
“[In China] they have very big facilities, they have the machinery, the people. But everything we produce is made in Europe and where possible, manufactured in-house by Roquet. Competitors make their parts in China and there’s a not inconsiderable price difference, so we sell on the quality of our products.”
Such is the focus on quality that it can take anywhere up to two years to bring a new cylinder design to market. Once in production, a 100% test cycle ensures that each finished cylinder is ready for a long working life in the field.
Quality focus
The focus on quality from Roquet is mirrored by the second company on our visit, Camac, a specialist in the design and manufacture of lifting equipment for passengers and materials.
Founded in the 1960s, initially as a manufacturer of concrete mixers and cable hoists, the company has refined its focus on elevation equipment such as rack and pinion hoists, elevators for materials and transport
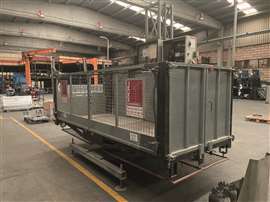
platforms.
Gabriel Jorba, managing and sales director, says its flagship product, the rack and pinion hoist, remains in high demand, but competition is high for such products.
Because of this, the ladder hoists range, while not a recent addition to the Camac range, is becoming an increasingly important part of its revenue stream. “The ladder hoists range is not so much for construction, it’s more for solar panel installers,” he says.
“In the last two or three years, we have invested a lot in this line. It’s very good for us. It’s not like the rack and pinion range with which we have plenty of competitors.”
The company says it has leaned into solar as it is an “emerging market” with strong demand.
However, the same cannot be said for the construction market in Spain, according to Jorba; “Currently the demand in the Spanish market is weak, due to two main factors.
“New building construction is weak, although the high demand and the deficit of available flats is strong. Rental fleets are full and very old (over 15 years), but companies are not renewing their fleets yet due to low rental prices.”
Some data from analysts say the number of new builds in Spain has gone down by 20% in the last year, with others predicting a further 25% decline in the future.
“A driver of the demand could be the speed up of new buildings, but at the moment it’s not like that,” Jorba says.
It doesn’t come as a surprise that as our visit ends, Jorba says that finding growth streams in an environment which makes it hard is a key target for the company in the future. What does surprise us is that he says the company is open to being acquired to enable this growth. Watch this space.
Global ambitions
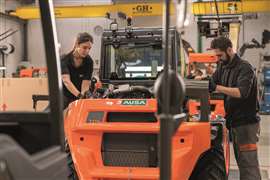
We finish off our trip to Barcelona with a visit to the headquarters of Ausa, a compact equipment specialist with subsidiaries in Madrid, France, the United Kingdom, Germany, the US and China.
In the context of the Spanish market, it is certainly one of the more well-known brands worldwide, and that recognition increased in May when the company informed it is to be acquired by JLG’s owner Oshkosh Corp.
That moves comes at a time when Ausa is seeing increasing growth opportunities in the US. “The US is becoming a big market for us,” explains Juan Urkijo Unzurrunzaga, commercial director.
“I would say that our second market is quite competed between France and the US, being this last one ahead at the end of June’s turnover. 75% of our sales are from Europe, with 20% coming from the US.” The company’s manufacturing operations are based in Spain, with as much as 70% of its manufactured machines exported via a network of more than 600 dealers.
But with increasing demand in the US and a new owner that knows the market well, could the company look to acquire facilities overseas to meet demand?
“We have a lot of room here to increase our production,” he says. “But we are also optimistic about significant growth in our sales in North America and Asia-Pacific, so when the time comes, we will see what actions we need to take to increase our production capacity.
“However, we are now beginning a new chapter in AUSA’s history and there is still a lot of discussions and a lot of synergies to look for from the production, sales perspective and network perspective.”
On the production line we are shown the company’s full range of equipment, including the JLG telehandler that it has manufactured here since 2020.
We are also shown its line of electric units, which have become a key part of its portfolio in recent years.
To date Ausa has focused its attentions on the lower range of equipment in terms of weight, which tends to lend itself to electrification.
“We are working hard in the factory to reduce our footprint, we have installed 1,200m2 of solar panels that reduce the CO2 emissions of the company by 35%,” Urkijo says.
“We are also investing in new technologies, and we have started to electrify models by taking advantage of a transmission we already have.”
The next step in that journey will see the company focus on electrifying new ranges of equipment, while long-term it will wait to see if technology can support bigger machines.
With the next edition of Bauma coming up in 2025, Urkijo also teases further electric developments in the future.
“If you look at our catalogue and see how compact our machines are, you’ll find out we have a lot of room to keep developing new zero-emission vehicles.”
The importance of rental
A trip from Barcelona to the picturesque region of Zaragoza takes us to Enar, a specialist in vibration equipment.
The company, a subsidiary of Wacker Neuson since 2022, was founded in 1964 and manufactures a variety of vibratory equipment, including pneumatic tools, power trowels and vibratory plates.
On arrival we are greeted by Jose Antonio Gomez Rueda, sales & marketing director; Jesús Tabuenca, research & development manager; and Rubén Sáez, export manager for Northern Europe, Africa, and Oceania.
“We started as a manufacturer of light construction equipment but have since added advanced vibratory equipment,” says Gomez.
As well as its product portfolio, it has also seen significant growth overseas. At the time of writing, it has a footprint across more than 100 countries, including South America, Asia, Africa and various European countries through its distribution network.
However, it is its home market of Spain that is the strongest, as Rueda reveals, “Spain is currently between the top 10 in Europe in construction equipment sales and is showing resilience in the current global scenario.”
In the context of Europe, he goes against the grain of others, saying that he believes Spain to be more solid than other regions, backed up by higher economic growth; “Inflation is forecasted to decline further. Demand on the residential sector remains high and renovation and civil works are also drivers at the moment.”
As for the future, the company told IRN that the rental industry will continue to play an important role in growth, while the acquisition by Wacker Neuson will enable it to continue its focus on “quality, innovation and growth.” One area it said it is looking to advance is sustainability, which is a key focus for its rental customers.
Through this advancement, the company will prioritise the manufacture of zero-emission equipment as well as reducing its own footprint.
Power play
A short journey across Zaragoza brings us to Carod, a company which originally focused on powered pumps for agriculture and fire protection, but now delivers a range of generator sets, high-pressure washers and
pneumatic compressors.
“The original plant was about 11km from here, but in 2011 we purchased this land and built this new headquarters,” explains Mohamed Mohinah, export manager.
He adds that while such parts as the steel genset closures are currently delivered by suppliers, there are plans to extend the facility and produce those in-house. “Covid was hard on our suppliers and lead times grew
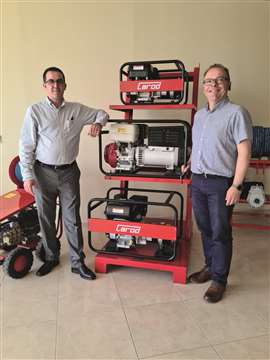
to nearly one year. So we’ll setup our own production to avoid any repeat of that.”
Since the completion of the new factory, Carod has been steadily ramping up the power output of its generators. “We’ve gone from about 250kVA to 800kVA,” says Mohinah. “We’ve got upcoming projects which will include our first 1MW gen set.” He adds that the production split at Carod is about 60% gensets, with all other products making up the remaining 40%.
Power for the generators comes from a range of suppliers, including Deutz, Volvo Penta, FPT, Honda and Kohler. In addition to these usual suspects is MWM International, part of the Navistar Group, which has its headquarters in Sao Paulo, Brazil. “MWM engines are all mechanical, no computers. That makes them very reliable, very rugged.”
Around the assembly hall, shelving units house hundreds of boxed engines. Mohinah says that they have more than $6 million in engine inventory. “It’s another result of Covid. We hold engines so we can quickly fulfil customer orders. If the engines in stock, I can fulfil a gen set order in about four to six weeks.” Inventory includes Stage 2, 3 and 5 engines with outputs up to 500 kVA.
Sustainability focus
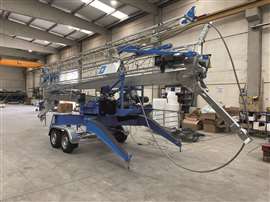
Just a short journey away from Carod is MiDi Cranes, a specialist tower crane manufacturer in the 3.5 tonne and below range.
That 3.5-tonne model, the LS15.17 RD, was launched recently; “This year with the LS15.17 RD we think we reached our largest capacity and reach crane with the limit of 3500Kg (3.5 tonne),” says Miguel A. Marin, deputy general manager when asked about potentially expanding into larger units.
“One of the projects that we have in mind to recover is the GT10 launched in the 60s. As the technology and capacities of cranes increase, they become more expensive.
“We believe that it may be a good idea to return to the simple idea of a small crane with more manual assembly, to achieve a cost/performance balance that allows us to enter developing markets.”
However, he is keen to point out that despite looking back to the GT10, its first design, there is plenty of room to grow as a specialist self-erecting crane manufacturer.
“We believe that it is a market to develop, which, without being the majority, is an attractive niche for us,” he says.
Outside of the facility, we are shown an old unit that the company toyed with during the economic crisis in 2008.
Despite never making the unit commercially available, Marin says that it is a symbol of the innovation within the company.
Expanding on his point, he says customers play just as an important role as engineers when it develops new machines; “In an F1 team, there’s the engineers working on the design and parameters of the cars, but driver’s feedback is crucial to get the best configuration of technology, since they are the one driving under complex circumstances.
“In our case, we have our engineering team that makes the design and calculations and factory test of the cranes, but the feedback of our customers, as heavy users of the cranes, is 100% taken into account to improve the ergonomics and use.”
Carving out a niche
We finish the day with a visit to Tarazona-based Tendo, a designer and manufacturer of steel scaffold systems.
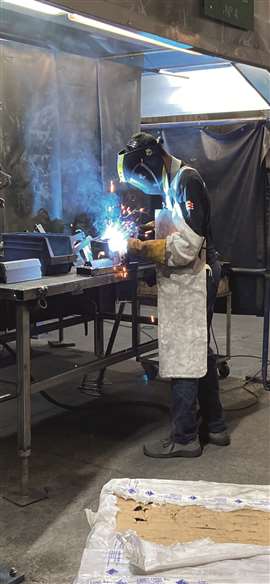
Founded in 1990, the company has been part of the Frénéhard & Michaux Group of industrial companies since 2016, which operates 24 sites across Europe.
Its two main products that it produces in Spain are the Goya and multi-directional ranges of scaffolding, while it also produces components at the Tarazona site.
According to the company, the easy assembly aspect of its scaffolding systems makes them an ideal solution for projects of any size across various industries.
Rental is also an important industry for the company, with its its simple structure and low requirements for training and assembly among the benefits to rental customers, it says.
At the time of writing, 80% of its business comes from the construction industry, while 20% comes from industrial industries such as the chemical, energy, fuel and food sectors.
Speaking to IRN, the company said it is one of a number of OEMs in Spain that are being impacted by the low number of projects in the country, but that is offset somewhat by its operations in North Africa and the Americas, helping it to generate revenues of around €6.3 million.
Meanwhile, it said the market in Spain is “waiting for the opportunity to invest.”
In terms of its relationship with customers, the company said it “actively works with customers” to provide tailor-made solutions for each project.
Tech development
Spain has a long history of manufacturing machines for construction, agriculture, mining, transport and power generation. But the country is also home to a series of technical institutes and universities which, in partnership with government agencies and related groups, are looking to develop new technologies intended to improve operational efficiencies across these and other industries.
Established in 1984, ITA (Instituto Tecnológico de Aragón) is a tech centre based in Zaragoza. Working with the Department of Economy, Employment and Industry of the Aragón government, the teams there are working on projects involving clean energy production, digital agribusiness and sustainable mobility.
In one such case, a team at ITA is working on the Ephyra project, or European Production of Hydrogen from Renewable Energy. This will see a 30 MW renewable hydrogen production plant integrated with a refinery in Corinth operated by Motor Oil of Hellas. This will deliver green hydrogen to the refinery and other external users as a test case for the circular hydrogen economy.
While development of this megaproject continues, ITA is continuing to develop mechatronics systems for both on- and off-highway vehicles, as Carlos Bernad, R&D project manager at ITA explains: “We’re looking at the integration of mechanics, electronics and robotics in machines with the intention of improving functionality across all areas. We’re looking for synergies between these fields, focusing on how mechatronics can support robotics and vice versa. It’s a little different from the standard perspective.”
While work originally focused on making improvements to existing components and machines, Bernad says that it is being involved with a project from the start which will help deliver the most benefit in terms of functionality and performance. For example, a project which was originally focused on robotics resulted in development of new sensors and related software, which ITA have now used to develop systems for different purposes.
In an outside testing area, Bernad presents a series of test machines, including a dumper and a medium-duty truck. Each features a different autonomous driving system developed specifically for the environments where the vehicles could be working.
With autonomous driving systems already available for such vehicles, Bernad is asked what’s different with those developed by ITA. “These systems have been adapted to harsh environments and specific tasks,” he says with clear enthusiasm. “With new advances in sensors and computational power they can process far more data, which makes them more efficient. The data capacity also makes the vehicles safer; they can react to dangerous situations with better decision making. The new sensors collect the data and then our algorithms use that information to make the best choice.”
Hitting heights
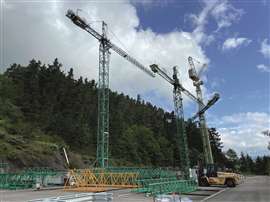
The final stop on our tour see’s us arrive in Idiazábal, where we visit a tower crane manufacturer, Jaso Tower Cranes
Founded in 1965, the companies range of cranes are used in a number of projects around the world, including waste management, energy, construction and railway.
Like some of the other companies on our trip, Jaso is at the mercy of the current conditions that the housing market in Spain finds itself in.
According to Theodor Peter Huitema, area manager, one issue is that cranes are currently being sent out for rental at “all time low prices.”
He says, “The paradox is that the demand for houses is in fact in there, but people cannot afford it at current price levels and high interest rates. The housing market besides is heavily conditioned by the surge in real estate prices because of an increasing number of vacation residences and foreign capital buying real estate.”
He says that high costs for materials is an issue facing other regions, in particular France, Belgium, Scandinavia and Australia, and stretches to “suppliers, rental houses and construction companies.”
Meanwhile, when looking at the scale of the Jaso manufacturing facility, it’s hard not to be impressed.
From the site the company distributes across the world, while it also has other production facilities in Spain and in India, Mexico and Argentina within the JASO group which is formed by Jaso Industrial, Jaso Elevation and Jaso Tower cranes.
It was only a few years ago that companies here were grappling with the supply chain crisis because of the pandemic. That, says Huitema, has eased; “As was the situation right after pandemic there is no shortage in the chain anymore. However, price inflation is still high in the supply chain which is still overcoming all type of hurdles to cope with the increasing material costs.
“It seems that cost increments have still not come to an end. Labour costs is one of them. Companies like Jaso are forced to increase their panel and look to guarantee the availability of materials in order to prevent any potential issue in the future.”
So, in the context of a challenging time for the construction market in Spain, it seems to be in a relatively strong position, despite an ever-apparent downturn in housebuilding. One thing that came across was that many of the companies we visited had or were looking to find new streams of revenue overseas, but not necessarily because the market in Spain isn’t strong.

Innovation too, seems to be strong among the OEMs. While some are choosing to find a niche, others are refining their existing portfolios to keep up with demand.
This article was produced with support from ICEX, the Spanish Institute of Foreign Trade, and ANMOPYC, the representative organisation in Spain for companies delivering technologies for the construction and mining industries.
A previous version of this article stated that Jaso is based in Pamplona, when it is in fact based in Idiazábal. IRN wishes to apologise for any confusion.