On the skids: loading in a 31,000 tonne module
06 November 2024
Brent Charlie, the last and largest topside module from the Brent field in the North Sea between the UK and Norway has been skidded to its final resting place for decommissioning.
The final load-in saw the massive steel and concrete structure skidded onto the quayside near Hartlepool, UK, from a barge. Brent Charlie’s journey started out in the North Sea, in the Brent oil and gas field, one of the largest out there, 186 km northeast of the Shetland Islands.
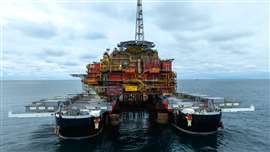
It was one of four platforms in the field. Brent Delta finished operating in 2011, then Alpha and Bravo production ended in 2014. Charlie was the last one, finishing in 2021. Mammoet already did the load-ins of the Bravo and Delta gravity-based topsides. Charlie was the third and the heaviest.
Skidding a 31,000 tonne topside onto the quayside was a major achievement in its own right. Adding to the challenge was its concrete legs that had been submerged in seawater for more than 40 years. “Careful engineering ensured the stability needed to carry out this operation safely and with precise control,” Mammoet said.
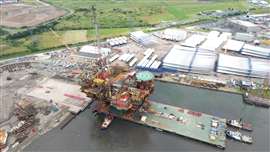
Same again
Removing and transporting Charlie from the North Sea to Able Seaton Port in the north east of England was pretty much the same process as for the previous topsides, “providing the peace of mind that comes from a tried-and-tested solution,” Mammoet said.
Offshore specialist contractor Allseas used its giant super heavy lift vessel Pioneering Spirit to lift the entire structure in one lift. It then transported it to shallow water and transferred the load onto the Iron Lady cargo barge.
Iron Lady was already set up with skidding equipment for offloading the topside at the port. Mammoet brought in 45 truckloads of materials for this, plus mooring winches. Allseas provided guidelines for the required lengths and drum load capacities.
With the loaded barge moored at the port it settled into the seabed. That gave the height and position needed for the skid tracks. Twelve skid tracks were installed to line up with the ones on the barge under the topside.
To start with the topside was skidded five metres to the rear of the barge. After leaving it for 12 hours to settle again the second stage saw it skidded 130 metres to its final position on the quay.
Skidding system
It was all done with a total of 76 skid shoes, divided between the platform’s four legs, and 40 hydraulic push-pull units. They all worked to move the load at a rate of 15 metres an hour. “The combined pushing capacity was 3,320 tonnes and the total lift capacity was 51,000 tonnes,” Mammoet said.
Prior to the move netting was put in place to collect debris and marine growth dislodged from the structure. Control of the move was carried out remotely to keep people safely away.
Stability of the four legged structure was one of the main challenges on this job. “When you look at stability, three legs are always stable; four legs are not,” said Richard Verhoeff, Mammoet sales director.
“You try to keep a three-point suspension when performing a load-in, and still need to achieve that even with four legs. That’s where hydraulic grouping comes in very handy.”
Deflection between the legs still happens, “so the force needs to be able to communicate between the different hydraulic groups.” To achieve this there were hydraulic cylinders under each leg and they were connected between both pairs of two legs to make sure the pressure on each could be kept the same.
Valid experience
“We have a pragmatic approach, which is required on jobs like this,” said Leo de Vette, Mammoet project manager. “It’s really a team operation, you must do it together. Time is of the essence, so equipment can be moved to the next job. Once the topside is on the barge, there is only one priority – get it off as safely and efficiently as possible.”