Outrigger pads: from the ground up
20 December 2024
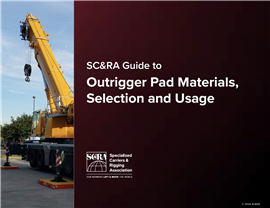
In an industry where safety underpins success, the SC&RA Guide to Outrigger Pad Materials, Selection and Usage is a vital framework for best practices in outrigger pad use across crane, rigging and specialized load-handling sectors, write Mike Chalmers.
It highlights essential industry topics that include the following: general industry awareness; lift planning; common products and solutions; and jobsite awareness. There is also explanation of pad setup.
The Specialized Carriers and Rigging Association’s latest publication, which made its first appearance at the 2024 Crane & Rigging Workshop event in September, carefully provides practical steps for assessing ground conditions and choosing the right pads to stabilise cranes and other load-handling equipment.
SC&RA said it stands as a testament to industry collaboration and knowledge-sharing. The Guide’s creation process involved an assigned task force of SC&RA member-experts from various companies and backgrounds. The size of the project meant the task force was itself broken up into smaller work groups, all the members of which contributed insight and experiences to build a shared resource that will elevate the entire industry.
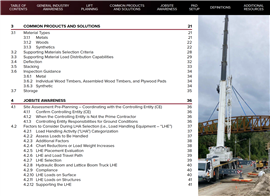
Ultimately, the group designed the document to address routine and complex jobsite scenarios and equip companies with tools to navigate the often-unpredictable conditions on which outriggers are deployed.
Jeremy Landry, president at specialist heavy lifting company Deep South in the USA, led the General Industry Awareness and definitions sections. “More than just cranes use outriggers,” he pointed out. “In everyday life, I notice load handling equipment without supporting materials underneath the outriggers all the time – concrete trucks, utility trucks and boom trucks.”
Landry felt it was important to help raise awareness, specifically for operators, to recognise poor ground conditions and have a general idea of how to mitigate their setup locations. “Specifically, the south is historically known for our poor ground conditions,” he explained. “At Deep South, one of the first questions we ask of our customers: is the site ground bearing allowable.”
He was also pleased to be a part of the collaboration. “This project was broken into sections because of its breadth, and working with members of this task force merely reinforced for me how knowledgeable people in this industry truly are. From the setup checklist for field personnel to lift planning for project managers, the guide we were able to develop gives balanced knowledge to effectively plan a job for any outrigger-based crane.”
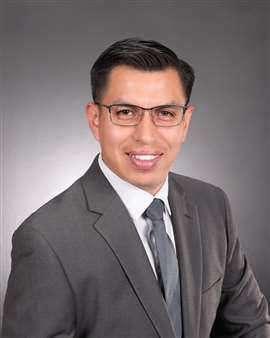
Practical framework
Christian Coronel, manager – engineering division at Bragg Crane in the USA, led the Lift Planning section, which emphasises standardised methods for pad sizing and load distribution. “The guide was crafted by those directly involved in crane operations, making it highly practical,” he said. “It’s designed to enhance planning across companies of all sizes – and with clear planning tools, this section speaks to safety, cost-effectiveness and consistency.”
What truly sets the Guide apart, said Coronel, “…is that it was developed by professionals who handle outrigger loads and ground assessments daily. We aligned it with ASME P30.1 standards to create continuity across the industry.”
Like Landry, Coronel’s contribution was fuelled by his desire to see industry-wide improvement. “At Bragg, we’re fortunate to have robust internal guidelines and technical resources but smaller companies don’t always have these tools,” he pointed out. “They often adopt practices that don’t serve the best interests of the crane industry, leading to potential safety risks. However, by sharing what we’ve learned, this guide offers accessible planning tools that create a safer, more informed industry.”
Overall, Coronel considered it a privilege to work alongside manufacturers, insurance representatives, colleagues and even competitors, for the good of the industry. To that end, he added, “My favourite sections are 1.6, 2.1.4 and 2.1.5. In these, we reference OSHA 1926.1402 and highlight the controlling entity’s responsibility for site ground conditions, including ground preparation and the allowable ground bearing pressure (AGBP).
“The guide provides clear guidelines on how the controlling entity can determine the AGBP, along with recommendations for situations where this information may not be readily available. These sections not only raise awareness about the critical responsibilities of the controlling entity, but also offer a practical framework for those tasked with determining and providing the AGBP value for safe ground conditions and crane operations.”
Filling the gap
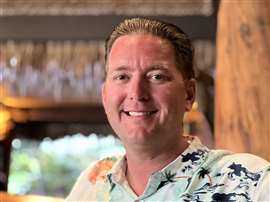
Tyler Elliff, president at Precision Crane Service in North America, joined the project to represent the operator’s perspective. “There wasn’t anything quite like this guide available before,” he explained. “We needed a practical resource that blends engineering with real-world usability.”
Without such a resource, he emphasised, companies have traditionally relied on “rule-of-thumb” practices rather than engineered solutions for pad selection, which can leave operators exposed to risk. “As a result, this guide fills a huge gap by making material choices understandable and applicable for people in the field,” he said. “It’s designed to help us recognise how simple, yet specific material choices can significantly enhance safety.”
Elliff gave particular credit to the Jobsite Awareness section within the Guide. “So many issues can be noticed, caught and mitigated simply by utilising situational awareness,” he recognised. “Additionally, the materials section covers various options, highlighting the strengths and weaknesses of materials commonly used in outrigger pads, and gives clear advice for inspection, storage and maintenance.”
Ultimately, he underscored, “If we can get this guide into the hands of everyone involved in the industry, we could prevent so many accidents.”
New standard
Kevin O’Neill, director of engineering at Bay Crane, agreed. “A guide like this helps bring that knowledge to all three areas of a company and helps promote safety. Early on in my career as a rigger, my supervisors said things like ‘Work smart, not hard,’ or ‘Plan the work, then work the plan” – phrases that speak volumes that I will never forget.
“Back then, experience was your education and is still invaluable to this day. However, for young lift planners or engineers, sometimes that experience is missing, and that’s where guides like this and others can provide the knowledge needed for a team to succeed.”
O’Neill also chairs the ASME P30.1 committee. He pointed out that the latest revision, due out in early 2025, has an entire non-mandatory appendix dedicated to the same topic – called Planning for Load Handling Equipment Foundation and Support.
“As you may suspect, I’m genuinely excited about the topic, and jumped at the opportunity to be a part of the SC&RA taskforce,” he acknowledged. “I was deeply involved with the Lift Planning and Job Site Awareness chapters of this guide.”
O’Neill reiterated that the writing of the guide is designed to be simplified, and not an engineering text. “We also tried to consider that several of the large crane and rigging outfits in the country may know most of what is presented in the document; however, we tried to focus on the small groups of lifting companies that make up most of the lift planning that can happen on any given day.
“It’s the crane owner that is also the operator, lift director and rigger – on the smaller jobs without the oversight – that a guide like this can really help to prepare better and ultimately work safer and smarter.”
Like Coronel, O’Neill took a liking to one section in particular. “The Load Handling Activity Categorization table in section 4.2.1.,” he said. “This table is from the P30.1 standard, developed in 2014, and provides a list for any lift planner to design how in depth the plan needs to be. Whether it’s a standard or critical lift, a written or simple verbal plan or perhaps a sealed engineered package, the categories provided help the team make better decisions on the task at hand.”
At the end of the day, he added, that’s what it’s all about. “SC&RA has a broad reach for promoting safe lift planning guidelines – a healthy membership of companies and several meetings. Getting information into the hands of knowledge-seeking lift planners is critical for the construction industry as a whole.
“This document is built on industry experience, giving planners and operators a shared criterion. And with a focus on practical knowledge and industry alignment, SC&RA has done a wonderful job here in providing guidance for load handling equipment safety.”
To access the document, see: www.scranet.org/membersonly