Powering up: how batteries are making tower cranes greener
11 September 2024
Hayley Arckless, UK country manager for Ampd Energy, tells Lucy Barnard how tower cranes are driving demand for its lithium battery energy storage solution Enertainer around the world.
Tower cranes are a common sight in the historic part of Birmingham city centre once known as the Gun Quarter.
In recent years, this part of the UK’s second city, once a centre for gun manufacture, has become the focus of building boom centred around student accommodation blocks catering to the city’s four universities.
Crown Place, a 33-storey tower with nine- and twelve-storey ‘shoulder blocks’ to the sides, on the city’s busy Lancaster Street, is no exception.
The tower is being built by Northampton-based contractor Winvic Construction with the help of a Potain MR 225A luffing jib tower crane supplied by lifting specialist Radius Group, also headquartered in Northampton.
Unlike most of the tower cranes dotting the Birmingham skyline, the Lancaster Street site and crane are powered, not by diesel generators but by a rechargeable battery supplementing power from the grid.
The battery storage system, known as the Enertainer – a portmanteau word combining ‘energy’ and ‘container’ is a 2.6 metre square, 7.3 tonne box which contains 30,000 lithium-ion battery cells – enough to store the energy needed to fill the energy peaks needed by up to three tower cranes.
Most modern tower cranes have been manufactured to run on electricity since the 1970s. And yet, their high power demand often makes it difficult for contractors to connect them directly to the national grid, even if there is a connection available. Yet, by using lithium battery cells to store mains power, the makers of the Enertainer unit say it is able to provide the short bursts of high power required for lifting loads.
Radius, which bought the unit as its first investment in energy storage systems to help power the cranes it runs, declined to say how much it had paid for the unit or how much it was renting it out for.
“We are seeing a significant and growing demand for alternative power solutions for tower cranes,” Rachel Swanston, marketing manager at Radius told Crane and Transport Briefing. “This is driven by the construction industry’s focus on sustainability and efficiency.”
And Birmingham’s Lancaster Street is by no means the only construction site using the technology.
Ampd Energy, the Hong Kong-based company, founded in 2014 which manufactures Enertainer units, has seen a massive surge in business since it started marketing its products at the construction industry five years ago.
The company, which started out making lithium-ion battery-powered backup power supplies for hospitals and data centres, has expanded from Hong Kong to supply units on a global scale.
Why is demand growing for battery storage solutions?
Today the company is active in Hong Kong, Singapore, Australia, North America, UK and the GCC.
“We are solving a very common problem that the global construction world is facing,” Hayley Arckless, UK country manager for Ampd Energy, told Crane and Transport Briefing. “We need to build and have the pipeline to do so but unfortunately, we don’t have the grid stability or availability to achieve this. Until now, the only other option has been diesel generators which are heavy polluters, high TCO and inefficient.”
“Our battery system was born out of specific demand from the construction industry for a unit that can handle the very niche requirements of power, as well as handle the tough environments on a construction site.”
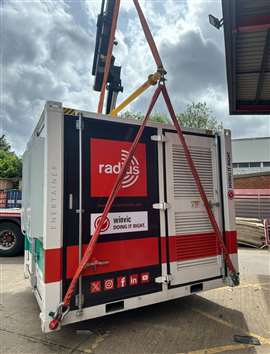
The company, a finalist in Prince William’s global environment Earthshot Prize, says every switch from a diesel generator to one of its units saves 130 tonnes of carbon dioxide a year.
“An Enertainer helps contractors use less power, more efficiently,” Arckless says. “It saves costs by taking a small trickle charge from a small power source (usually grid) which negates the need to wait for costly grid upgrades, renting generators, bowsers, and other technologies, not to mention that it can eliminate the huge diesel or biofuel bill altogether.
“Batteries also add an extra level of power security to a site, meaning sites don’t need to worry about generator breakdowns, or grid outages,” she adds. “Storing energy in an Enertainer to use efficiently means if there is an outage in the original power source, sites can keep working to ramp down safely.”
As Arckless readily admits, as a battery storage solution, the Enertainer is only as sustainable as the electricity which it stores – something that can differ significantly depending on how much electricity each nation produces from renewable sources such as wind and solar power and how much comes from burning gas, oil and coal. Enertainer is charged at a rate of between 10 and 80 Amps from a 320 to 440 Volt three-phase AC mains supply.
“Batteries are considered new technology, but this is a myth,” she says. “We have been using battery storage technology for decades in utility scale grid support, in electric vehicles and more. We are simply extending the use case of this technology into an industry which can really benefit from it.”
Of course, Enertainer units are not the only option for contractors looking to reduce the carbon footprint of the tower cranes they use on site. Manufacturers are producing a full range of technological solutions aimed at removing or reducing the use of diesel generators on sites. These include: far more affordable flywheels which can flatten out electricity demand on generators by storing the sudden spikes in electricity needed by tower cranes for lifting loads as kinetic energy; and battery storage solutions made from lead-acid batteries.
What are the alternatives to battery storage solutions?
“We don’t see ourselves as competitors to the technologies listed above, mostly because we can solve multiple problems and can power the vast majority of a construction site,” Arckless says. “A flywheel for example, is a great technology for peak shaving and reducing a fuel bill on one piece of equipment. A lead acid battery might be good for small levels of stable load requirements like overnight lighting or cabin welfare, but the lifespan is much shorter, and it needs to be paired with an equivalent sized generator to power high loads like a tower crane, so saving opportunities are limited.”
Yet, as the construction industry continues to look for ways to decarbonise, Arckless says that, in the future Enertainer units could be used alongside hydrogen generators or fuel cells.
“Hydrogen is a very interesting technology, but unfortunately it is quite cost prohibitive at scale,” she says. “However, we think we can solve this barrier to entry by working together. Pairing a battery with a hydrogen generator as a power source, enables the user to significantly downscale the generator size to as low as 75 kVA, creating a fully zero emission and low carbon power solution for construction.”