What are the latest developments in quarrying equipment?
23 August 2024
The quarrying sector is pushing ahead with the development of many innovative features and solutions. Catrin Jones takes a look at some of the latest and greatest on the market.
The UK’s construction, quarrying, and recycling trade show, Hillhead, which took place over three days in Buxton earlier this summer put the some of the latest developments in quarrying equipment firmly under the spotlight.
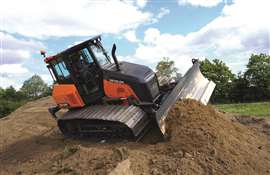
The event, which showcases a variety of large equipment for the European market, attracted 26,626 visitors throughout the duration – an 8% increase from 2022.
One of the central themes of the show was the increasing demand for sustainable, safer, and technologically-driven equipment. While other sectors are catching up, the quarrying industry seems to be driving a considerable amount of innovation, making significant advancements in solutions that impact the way operators work and enhancing safety.
Machine debuts
Making an entrance into the European dozer market is Develon with the launch of the new DD130-7, highlighting its work to enhance safety on machines. The DD130-7 offers a productive fine-grading solution for residential and light commercial construction projects, as well as enhanced visibility of the machine’s dozer blade.
To facilitate this, Develon says that the front engine compartment offers a narrower design and is combined with other features that make it easier for operators to see their work.
A standard rearview camera provides operators with an additional view of the dozer’s surroundings for further visibility and safety. The full-colour, 8-inch Smart Touch display shows the feed from the rearview camera.
Standard features include high-illumination LED lights and four premium wiper blades. The DD130-7 prioritises comfort with a high-quality premium seat as well as the seat and joysticks move together via the air suspension system, absorbing vibrations.
Big launches at Hillhead
Using Hillhead to launch one of their biggest crawler excavators yet, HD Hyundai Construction Equipment announced the arrival of the 80-tonne HX800A L and the 100-tonne HX1000A L.
The heavy-duty machines are designed to operate in mines and quarries, as well as in bulk earthmoving for construction and infrastructure project applications.
The HX800A L uses the six-cylinder Perkins 2506J, providing 400kW (539hp) at 1,800rpm and 2,468Nm of torque at 1,400rpm. The larger HX1000A L is powered by the Perkins 2806J, offering 460kW (629hp) at 2,000rpm and 2,952Nm at 1,300rpm. An electronic hydraulic power control system minimises fuel consumption while increasing digging efficiency. It utilises nine sensors across the machine to calculate the required flow and pump output and optimise efficiency.
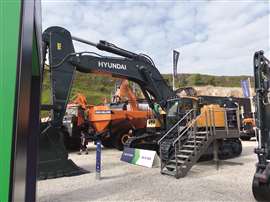
Also launched at the show was the HX800A L loader. The company highlighted that the machine adopts the same design and components of the smaller A-Series machines.
Powered by the latest Cummins X12 diesel engine, the six-cylinder EU Stage V compliant motor delivers 321kW (430hp) of power at 2,100rpm and 2,300Nm of torque, from just 1,400rpm. That is 10% more power and 20% higher torque than previous non-Performance Series engines, despite lower fuel consumption and exhaust emissions.
The loader benefits from an Eco gauge within the cab that monitors fuel consumption in real-time. This allows the operator to see fuel use, engine torque, average efficiency and total fuel consumed, enabling more efficient operation of the machine in varying conditions. A Smart Power mode further reduces fuel use, by adjusting the engine speed while loading the bucket. This also balances traction, for improved productivity.
Pushing new limits
Having made progress in innovative and advanced quarrying equipment for more than 60 years, Austria-based SBM Mineral Processing highlighted its Remax 600 impact crusher at Hillhead.
SBM Mineral Processing officially released the mobile crusher in 2023 but its UK debut was at Hillhead.
The company says more than three years of intensive research and development has gone into the Remax 600 impact crusher, in hopes of setting new standards in process automation and paving the way for AI-based autonomous crushing.
The mobile crusher and its AI capabilities highlight that even large-scale activities at quarries and mines can be made safer by omitting the role of an operator.
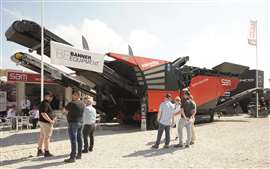
Micheal Brookshaw, global distributor development manager at SBM Mineral Processing, suggests that over time, these machines will only become smarter as they adjust to learning and recognising behaviour patterns in their work.
Every five seconds, data is transferred from the machine to the digital twin into the database and then back to the machine, says Brookshaw.
He adds, “The machine will be completely automated and adjusting itself but as we go on, the machine and the system start to learn. The more crushers we have got into the system, the more accurate that digital database is getting. In two or three years you will be doing it on your desktop.”
Furthering automation
Another technology venture for the sector has been launched between four companies aiming to future-proof the effectiveness and competitiveness of quarrying operations within the minerals and aggregates industry.
The companies – Chepstow Plant International (CPI), Bell Equipment, technology platform specialist, xtonomy, and global materials solutions company Sibelco – are working to produce an autonomous articulated dump truck (ADT).
The new autonomous solution was initially launched at Sibelco’s quarry in Devon, UK, with a full demonstration of the new autonomous solution within a working quarry setting, but was recently shown at Hillhead.
The hardware, supplied by technology platform specialists xtonomy, includes radar sensors, GPS, multi-channel communication systems, and on-board processing hardware.
Further benefits associated with autonomous trucks include extended component life, reduced wear and tear, and environmental advantages due to improved fuel efficiency from enhanced operational efficiencies.
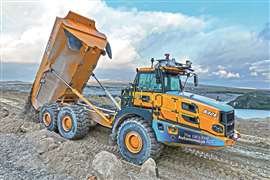
“CPI’s autonomous B40E takes environmental benefits a step further by using HVO fuel instead of diesel, making the machine ‘almost carbon neutral,’ which is a significant achievement in the current quarrying and mining industry,” says Brad Castle, product manager at Bell Equipment.
“We’re pleased by how our autonomous ADTs have enhanced operational efficiencies on the sites where they are working by being able to operate for longer periods, deliver really accurate tipping results, and improve productivity.”
The combination offer a navigation system that plans ADT paths and predictively controls the vehicle around the entire quarry site.
The pilot scheme aims to demonstrate the potential to reduce vehicular incidents and subsequent accidents as well as upskilling the existing workforce to further support the future of quarry operations.
When choosing to operate a Bell ADT autonomously, customers have the choice of third-party suppliers and the level of autonomy they want to achieve.
In this regard, Castle adds, “Along with Xtonomy and Pronto AI, we have recently started working with UK company, ABD Solutions, and Steer, a Norwegian company supplying autonomous haulage solutions for quarries and mines, as well as with American-based Teleo, which is working on a remote-control conversion of a Bell ADT.”
Profound transformations
Julie Andras, marketing director at screening, pelletizing & primary crushing systems provider Haver & Boecker Niagara, agrees that the quarrying equipment industry is witnessing profound transformations driven by automation and digital technology advancements.
“The importance of AI in the quarrying and aggregates sector cannot be overstated,” she says.
“We are seeing technology impact the development of quarries to optimise their efficiency. Quarry operations are also turning to software to help plan what equipment they need – such as vibrating screens – from machine placement and plant flow to product pre-calculations.”
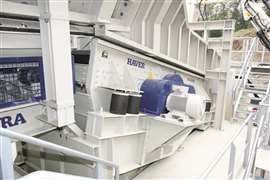
Andras adds that in addition to artificial intelligence and other software systems, the industry has a growing demand for advanced diagnostics technology. Operations must ensure that their equipment runs at peak performance to avoid unforeseen downtime. Equipment breakdowns and malfunctions are a significant source of lost revenue for aggregates producers.
The Canada-based company developed Pulse Condition Monitoring (CM) for vibrating screens to help quarry businesses increase their machine uptime without constantly having to analyse the performance of equipment themselves.
Andras highlights that Pulse CM is a wireless diagnostics tool that helps mineral processing operations be proactive, rather than reactive, in maintenance efforts.
“It captures real-time information on equipment and provides email alerts when it detects the first sign of potential problems,” she says.
“By constantly monitoring the accelerations of the vibrating screen, Pulse CM provides a forecast of the equipment’s dynamic conditions in several different intervals – 48 hours, five days, and four weeks. It detects anomalies that alert an operation’s maintenance team to certain areas of the equipment that may require attention.”