The art, science and economics of a lift plan
03 September 2024
Over the past 25 years, lift planning has greatly evolved. The biggest change in the realm of lift plan development is the advancement in lift planning software, which allows users to choose many variables when planning a lift. With this software, a lift planner can choose the crane and rigging, determine the ground bearing pressure and assess everything that needs to be considered at the site. Small and large crane companies regularly use lift planning software to plan and execute lifts, from simple lifts to highly complex, engineered lifts.
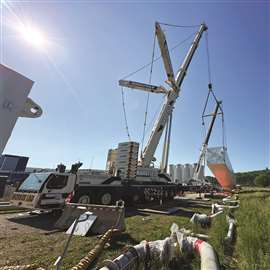
Lift planning adds value in a number of ways, including enhancing safety and risk management. There is an economic component as well. Lift plans offer a company a competitive edge when bidding a job. More and more, lift plans are required as a part of the bidding process.
To discuss the evolution of lift planning, American Cranes & Transport convened a panel of three professionals to discuss lift planning processes and procedures in their company. The panel includes Alex Clark, regional general manager for Omega Morgan; Trapper Wyman, president and head of estimating and planning for Mansfield Crane Service; and Larry Smith, general manager of Wilkerson Crane.
What does lift planning bring to the table in terms of doing business in the markets you serve?
CLARK: It brings a level of professionalism that our customers like to see. It also helps to visually show how we have thought through the project for our customer by helping them see the crane on the site on a 3D Google overlay or on a site plan drawing.
Wyman: It allows us to show our customers how we will set up the crane and perform the lift. For a lot of people not in the crane industry, it’s hard to visualize what the crane will look like onsite and other specifics like the direction it’s going to swing. We are giving them the picture of how it’s going to look when it happens.
SMITH: We utilize lift plans on a daily basis. A lift plan gives us an opportunity to layout setup locations on a jobsite accurately, not only for our crane operators to reference, but for our customers to be able to use when planning with their trade partners for a crane to be on a jobsite.
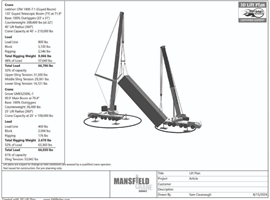
What types of jobs constitute a lift plan in your organization?
CLARK: Almost every project that we do now requires some level of lift planning. Currently, almost every large contractor requires a lift plan. Industrial projects always require a lift plan, and any high value item requires a lift plan.
WYMAN: We use the ASME B30.5 standard, and many times we use our customers’ standards that we have adopted. Each job that comes in, the type of lift gets categorized as standard or complex. A standard lift is a lift where there are known loads, and rigging and is a standard operation. With complex lifts, there is an element of special load handling activity, maybe rotating horizontal to vertical using a crane and another lifting application.
Based on the lift categorization, that will determine the type of lift planning involved. Under the ASME standard, you can verbally have a lift plan on site. The operator might do an onsite lift plan for a standard lift. But a lot of customers want a pre-written, predetermined lift plan for the job. We prepare a lift plan and the drawings that go with it and give it to the customer prior to the job so that the customer knows how it is all going to take place.
Sometimes the customer will want an engineered lift plan, and sometimes we will want to have an engineered plan. This is when a licensed engineer looks over the plan and stamps it.
We primarily use 3D Lift Plan. We also use Auto Cad for the rigging diagrams and other software to mark up the plan with additional information. Our entire fleet is logged into the 3D Lift Plan software.
SMITH: Wilkerson uses lift plans for almost every job you can think of. We often make them for our equipment rigging and moving guys to be able to strategically plan how they are going to move large equipment on different jobsites. We also make them on a daily basis for our crane jobs, no matter how big of or small of a crane it is. A lift plan helps our operators and sales staff accurately layout and setup the jobsite, as well as move our cranes into the jobsite.
Do you use lift plans to help with bidding or estimating a job?
CLARK: Yes, we do send lift plans for some jobs that we are bidding to let our customer see that we have thought this project through. It helps ease some of the concerns that they may have with using our company or a crane in general.
We feel like it can also elevate our chances of winning the project over a competitor as it lets our potential customer know that we have thought this through. It can also show any issues that the customer has not factored in until they see the drawing.
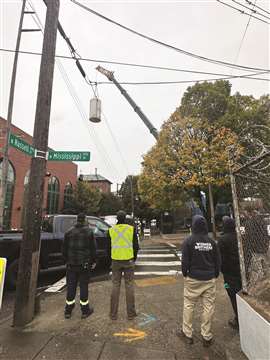
WYMAN: We use lift plans in the planning process, when we are doing the estimate for the job. We will lay out the plan ahead of time. It helps us determine the best place to situate the crane to give the best capacity and not have to move the crane, or assure that we move it a minimal amount. We can use a Google image of the jobsite and put the crane in the image to see the best place for it. It helps us make sure we are not sizing a crane that is too large, so that we give the customer the best price.
SMITH: Yes. Often times a customer will call needing a quote, and a site visit isn’t possible to complete before a bid needs to be turned in. With lift planning software, we can ask our customer a few simple questions and setup a lift plan based off the data we collected to make an accurate lift plan and estimate.
Can a lift plan actually enhance safety at a jobsite?
CLARK: Yes, 100 percent. On certain jobs we sit down with our employees and go over the plan with them. This helps everyone understand the challenges we are facing. We also send them out with our dispatch work orders so that our crews have an understanding of what we are doing and what configuration the crane is in. It also helps when they get to the site to double check it matches what the site looks like compared to the drawing. Site conditions can change quickly.
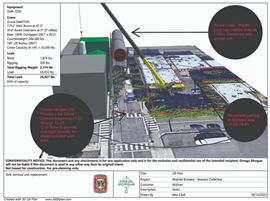
WYMAN: Yes. The lift plan is not just about what you are lifting, it’s also identifying any hazards, energized lines, underground utilities or constructions. It can be a good risk assessment. Also, an important part of a lift plan in the field, is a competent person uses it to identify a change in conditions. These people have the ability to adjust the plan and further communicates to the customer the changes that are made.
All the cranes we own are in our 3D Lift Plan software, so we can see all the configurations possible with each crane. We use Auto Cad for the below-the-hook rigging – slings, shackles, spreader bars. There’s nothing we can’t represent.
The lift plan has certainly evolved through the years. Twenty-five years ago, there wasn’t any kind of framework for a lift plan. A lot of customers have built their own framework. We’ve adapted that where we find it most useful. Today, I’d say 90 percent of our customers require a prewritten lift plan. It’s a critical part of doing business. We develop a lift plan for pretty much every job we do.
SMITH: Yes. With a lift plan a customer can see where a crane is going to be placed onsite. They can help direct us about underground obstructions that we may not know about or reveal reasons why we might not be able to setup in a chosen area. The lift plan also lets site personnel know where a crane is going to be setup, the lifting radius and the danger zones. With the danger zones, we may need to keep other personnel, or even the general public, out of an area where we may be lifting or where crane setup will occur.