Airships for construction have failed before. Could they take off this time?
27 November 2024
A new generation of companies are hoping to bring airships to the construction industry to use as both floating cranes and cargo carriers. It’s a good idea on paper, but will it fly? Lucy Barnard finds out.
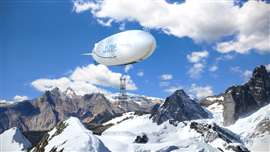
Imagine a future where rather than assembling crawler cranes on a construction site, loads could be lifted by a hook in the sky set to whatever height was required. Where rather than trucking prefab buildings and heavy supplies to site, they could be lifted serenely by air and gently set down when required. And where construction and maintenance in remote mountainous or offshore locations could be handled from the sky with zero emissions.
That’s the pitch for a new generation of companies hoping to bring engine-powered hot air balloons - or airships - to the construction industry to use as both floating cranes and cargo carriers.
Floating cranes
“We’re removing a roadblock in the logistics challenge of lifting and transporting heavy things,” says Jeremy Fitton, founder and CEO of SkyLifter, one of a number of start-ups looking to raise money from investors to build lighter-than-air craft aimed at the construction sector. “When you’re air-lifting more than 20 tonnes vertically, there are no other practical solutions.”
Certainly, if easy-to-hire dirigibles could be used in construction, the benefits are clear. Once inflated, so-called lighter-than-air craft consume relatively little fuel, potentially making them the ideal vehicles for lifting heavy loads in spaces which cranes find difficult to access or for carrying unwieldy loads such as wind turbine blades or prefab buildings.
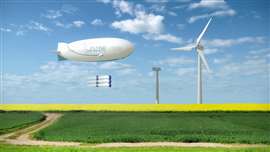
What’s more, airships are usually filled with either hydrogen or helium and can be directed using electric motors, making them an extremely low carbon method of lifting and moving hefty components.
With no requirement for expensive ground infrastructure like airports or roads and few fuel requirements whilst airborne, it could be relatively cheap to have one hovering around in the sky above a site, helping with lifts or waiting to offload cargo without getting in the way.
And, as a tried and tested technology which has been around for more than 150 years, regulations for flying airships are well established in most countries.
For Fitton, it’s an innovation with the potential to revolutionise the entire industry.
How could airships revolutionise the construction industry?
“If you introduce a capability to lift and move oversize or fragile payloads, from and to any location, suddenly that changes the economics of construction,” he says. “It frees up the industry to make things even bigger. You can make a roof-truss in a different way because you don’t have to dismantle it into smaller pieces at manufacture and put it back together again on site. You can make it cheaper because you can make it in one big piece.”
Fitton’s SkyLifter has so far built a couple of smaller prototypes of its flying saucer-shaped balloon and is currently looking to raise the cash to build a larger model with the capacity to lift up to 2 tonnes.
Further along on its fund-raising journey is France-based Flying Whales, which is backed by the French and Quebecois governments as well as firms including Bouygues Construction. The company closed its third equity fundraising of €122 million (US$129 million) two years ago and is looking to raise even more next year order to start flying its 200-metre-long LCA60T airship in 2028.
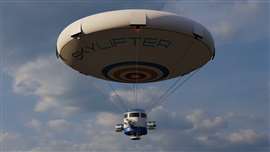
Flying Whales says that its airships will eventually be able to carry weights up to 60 tonnes, enabling construction teams to simplify projects such as installing power lines in remote areas – something that currently requires pylons to be divided into sections and then transported by helicopter section by section.
“The Flying Whales transport solution will allow Eiffage to rethink its organization of construction sites in remote areas, reduce its carbon footprint, improve factory design and optimize logistics preparation and reduce on-site assembly operations,” says Richard Hellstern, sales manager at Eiffage Energie Systemes, another large French construction firm which is lending its support to the company.
The company’s European sales manager, Laure de Laforcade, says construction is a key area of focus for Flying Whales, especially in areas which are difficult to get to by road and that the company is already engaged in active discussions with a handful of French and international building firms about using the technology once it becomes available.
Los Angeles-based Aeros, which traces its roots back to the Soviet Union, already designs and manufactures airships for advertising, broadcasting and military uses. Last year it announced it had come up with a design for its cargo airships allowing them to overcome one of the major hurdles currently bugging most manufacturers – how to compensate for weight changes when loads are picked up or dropped off – by sucking in and pressurizing air.
Yet the history of airship solutions for carrying cargo is a long one and riddled with corporate failures.
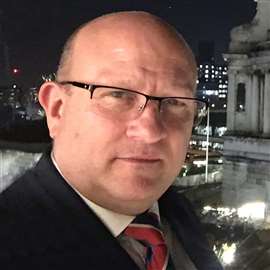
Back in the 1950s Goodyear Aircraft Corp came up with plans for a dynamic lift airship capable of transporting heavy loads while similar concepts were proposed and patented throughout the 1960s and 1970s. However little progress was made, due to both the costs involved and overcoming the technical challenge of adjusting the buoyancy of the craft to allow it to pick up and drop off deliveries without releasing the high-value lifting gas.
In the early 2000s German heavy lift airship company Cargolifter, an airship company founded by a group of influential engineers and scientists and based at the Brand-Briesen airfield in Brandenburg, promised to launch commercial services for transporting heavy and bulky goods to remote places by 2005. In fact, the company filed for insolvency in 2002, and its hangar was later converted into the world’s largest indoor water park.
Airship specialists point out that the reasons that most of these past ventures failed is nothing to do with the airworthiness of the craft. As the first aircraft capable of powered flight, airships were more commonly used than passenger aircraft before the 1940s but their use decreased following the high-profile Hindenburg disaster in 1937 and as their capabilities for speed were surpassed by those of planes.
Instead, they say, most ventures have failed due to the high cost associated with building, maintaining and operating the ships, and due to the fact that other forms of technology have been able to carry loads either quicker or more cheaply.
“The technology is all there. The actual physical engineering way of doing this is already known and proven,” says SkyLifter’s Fitton. “The reason the skies are empty is not for the sake of the technology or the materials or any of the supply chain.”
Why have previous attempts failed?
“It boils down to the fact that there’s a disconnect between the way the technology is engineered and the way the customer can possibly adopt it. And that really starts with understanding that the customer actually wants a hook in the sky. The industry keeps trying to build the best airship when in reality they should be making the best hook.”
Fitton initially came to the industry hoping to find a way to move outdated pressure vessels and other heavy equipment from remote mining sites in Australia.
He says that increasingly strict emissions targets are helping to tip the scales back in favour of airships becoming commercially viable - principally due to a potentially huge demand from windfarms – a sector already garnering considerable government support.
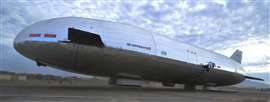
Aeros calculates that currently, the cost of carrying one large turbine blade by conventional means can exceed US$370,000 while its Aeroscraft airship would be capable of carrying three 85-metre blades in a single trip, generating approximately US$1 million in revenue for the company.
“We see an existential crisis in the wind industry,” Fitton says. “They want higher and higher turbine towers, placing them further and further away from the shore or in more challenging and remote locations on land. And there is currently no practical or scalable maintenance solution. There are lots of ideas but no cost-effective or sustainable solutions. And the wind sector needs to present a solution to institutional and government investors in order to continue to attract the investment needed to deliver on the transition to green energy.”
Sceptics will say that similar things have been said before and ultimately amounted to just a lot of hot air. Yet optimists will point out that perhaps, just perhaps, this time there is an opportunity for airships to provide the industry with a much needed lift.